Correct welding of flame tube and smoke tubes
The connections between the flame tubes and smoke tubes and the base are one of the most sensitive areas in high-pressure boilers. These connections must be able to withstand high stresses and temperatures. At Bosch, smoke tubes are therefore welded in by state-of-the-art robots and semi-automatic welding systems are used for flame tubes. Particularly homogenous and robust connections are obtained by carrying out welding fully or semi-automatically. Cooling grooves are also used on the water side at weld seams that are exposed to high thermal stresses. Particularly for thicker sheet metal this provides excellent cooling even in high load condition.
Burner passages however are made without water cooling in order to increase the boiler’s durability. Complicated and costly repairs including a complete hydraulic pressure test are thus prevented. Thanks to Bosch’s special insulation concept in the burner passage, heat emission losses and heat input of our industrial boilers can be minimised. This also increases the robustness and ease of maintenance of the boiler as the insulation material is designed to last the entire service life of the boiler when commissioned and operated correctly.
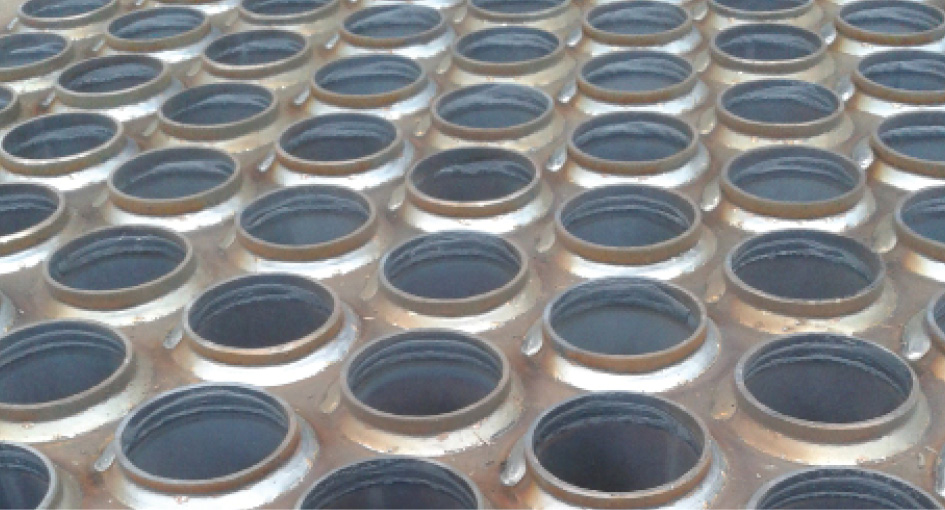