Water treatment
Correct water treatment is one of the most important fundamental prerequisites for safe and long-term operation of a boiler system. Strict requirements therefore exist in relation to the water quality of boiler systems.
The terms used in connection with boiler systems and their corresponding synonyms for the various water flows are explained briefly below.
Term |
Explanation |
Freshwater (raw water) |
Untreated water that is obtained from the following sources:
This water is fed in to fill the system and replenish water lost and is normally admitted at temperatures of around 10°C. |
Softened water (hardness-free water, |
Water from which calcium (Ca2+) and magnesium ions (Mg2+) have been removed using an ion exchanger. |
Partially demineralised water (permeate or |
Water which contains more or less no salts. It has a conductivity of < 50 µS/cm and is normally recovered from softened water by reverse osmosis. |
Demineralised water (deionised water) |
Water which contains no salts whatsoever. It has a conductivity of < 1 µS/cm and is normally obtained by a combination of anion and cation exchangers. |
Make-up water |
Softened, partially or completely demineralised water which is fed into the feed water vessel for deaeration. |
Oxygen-free condensate (high-pressure condensate) |
Condensate which accumulates in closed tanks at pressures > 0.2 bar. |
Feed water |
Softened, deaerated and chemically conditioned water which is fed to the boiler via feed pumps. |
Terms for the various water flows with explanations
Errors made during water treatment, in the analysis accompanying the water treatment and insufficient monitoring of water quality are still the most common reasons why operation is disrupted or the steam boiler system is damaged.
For this reason, wide-ranging rules and regulations have been adopted at European level which precisely define the requirements for feed water and boiler water quality.
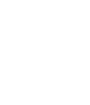
EN 12953-10 sets out specific guidelines for the appearance, conductivity, pH value, overall hardness, acid capacity and iron, copper, silicic acid, oil/grease, phosphate and oxygen concentration. The water should also be free of organic substances. |
Technical report: modern water treatment and water analysis
These requirements in relation to the feed water admitted to steam boilers and the boiler water lead to the reduction or elimination of the following causes of damage and faults:
- Corrosion
- Deposits on the water side
- Foaming of boiler water
- Sludge formation
The freshwater must be treated to ensure that the water values are complied with and thus avoid damage due to an increased concentration of problematic substances in the water.
Various measures are taken during the water treatment, depending on the output of the boiler system, condensate accumulation rate and ingredients in the available freshwater, to ensure the water is suitable for use during boiler operation.
The following illustration provides an overview of the contents of freshwater or condensate, the dangers they pose to the steam boiler and boiler system and the corresponding water treatment measures that must be taken.
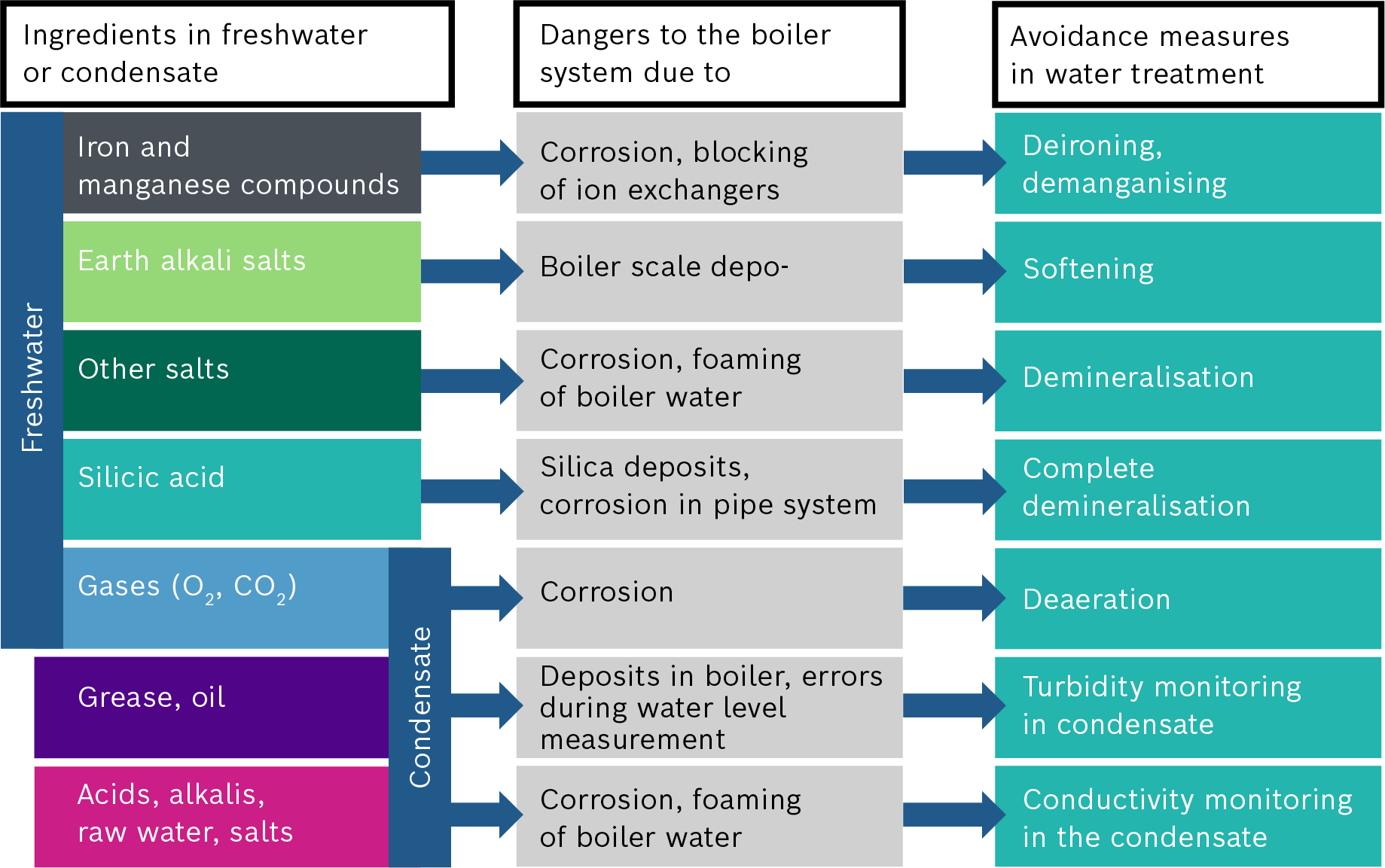
Ingredients of freshwater and condensate
The starting point for designing a water treatment system should always be a detailed analysis of the available freshwater quality.
Deironing and demanganising
During deironing and demanganising, iron(II) (Fe2+) and manganese(II) (Mn2+) ions dissolved in the water are initially oxidised to form higher-quality ions. The oxidation can be carried out using oxygen (O2), other oxidising chemicals such as potassium permanganate (KMnO4) or via catalysis. The resulting by-products are subsequently filtered off via a filter granulate.
Softening
Among the substances dissolved in water, hardness is especially harmful to the operation of a boiler system. Hardness mainly comprises calcium and magnesium ions (Ca2+; Mg2+). If these so-called alkaline earth metals are present in the feed water, they can precipitate due to the heating in the boiler and form limescale which is deposited as a layer on the heating surfaces.
If the formation of a layer or coating is not identified early on, this will lead to a deterioration in efficiency because the heat transfer is restricted. If the layers continue to thicken, this can lead to overheating of the heating surfaces and damage with serious consequences, which could also mean a total loss of the boiler.
To prevent this, the hardness components must be removed from the water.
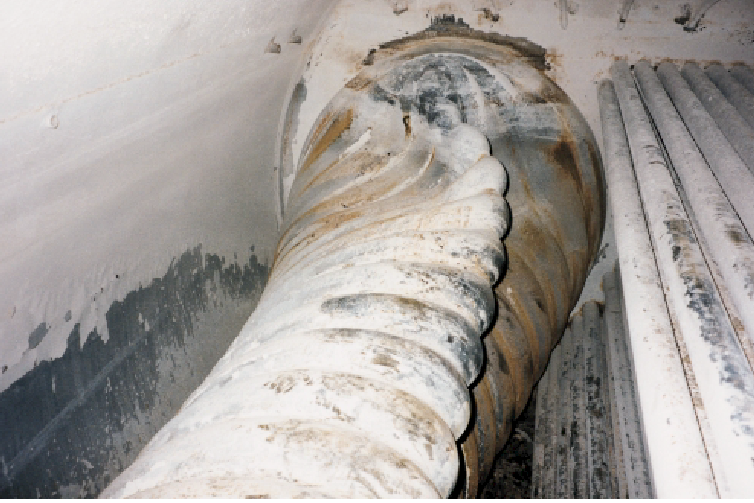
Layer formation in boiler with damage to flame tube
Operating principle of ion exchanger
Ion replacement is the most common water softening method. This involves replacing the hardness-forming substances calcium and magnesium with sodium, which is harmless. Ion replacement is a straightforward and efficient water softening method which involves only the small cost of using special regeneration salt.
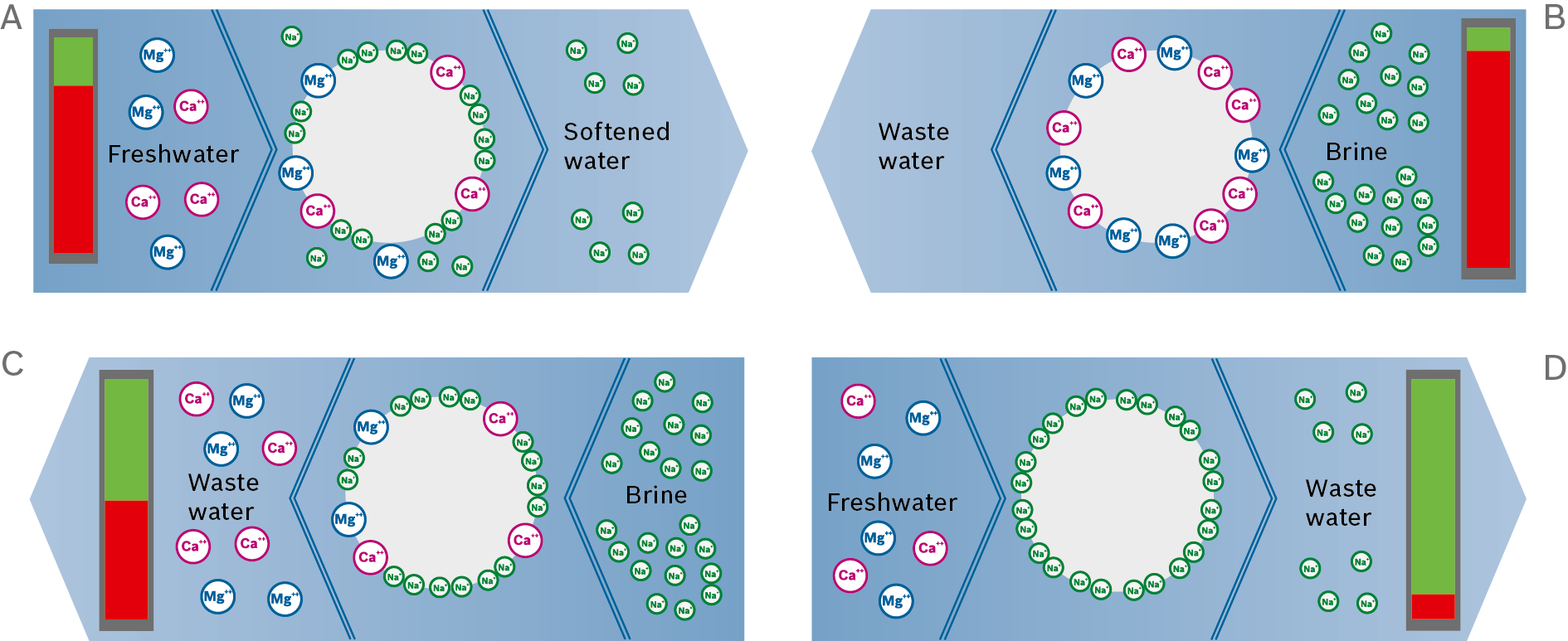
Operating condition A: softening of water
A chemical balancing reaction occurs during water softening through the exchange of ions. Sodium ions adhere to the exchanger resin in the pressure tank. When the calciferous water flows through the water softener unit, the calcium and magnesium ions in the water are bonded to the exchange resin. Sodium ions are released in exchange.
Operating condition B: start of regeneration
The exchange resin continues to accept new hardness components until it is saturated. The ion exchange resin must then be regenerated. Special softening salt is required for this which dissolves in water to form brine.
The exchange resin is flushed with the brine during regeneration. Due to the surplus sodium in the brine, the resin releases the calcium and magnesium ions once again and absorbs sodium ions.
Operating condition C: end of regeneration
As the resin primarily binds calcium and magnesium ions to it, it cannot be fully regenerated. It is therefore recommended that only water softeners with so-called economic brining are used.
Operating condition D: softening of water starts once again
Once the regeneration process is complete, the ion exchanger is flushed with water and is ready for another water softening cycle.
With larger water softener units it is recommended that dual systems are used. These can be operated on an alternating basis.
In this way one ion exchanger can produce softened water while the other regenerates. Thus it can be ensured that softened water is always available.
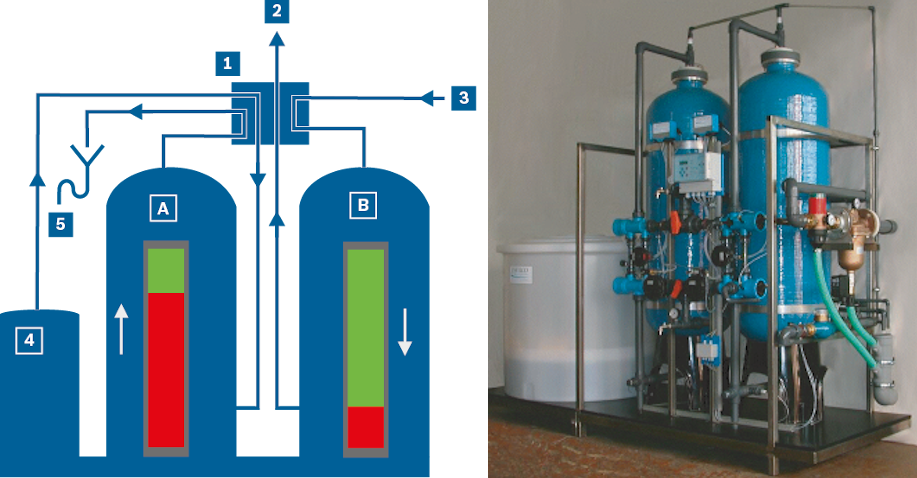
Schematic and visual representation of a dual water softener system
|
Operating condition A: ion exchanger is regenerated |
|
Operating condition B: ion exchanger in operation |
|
Changeover fitting: showing current flow direction |
|
Softened make-up water |
|
Freshwater |
|
Container for regenerating solution |
|
Waste water |
Demineralisation
Water in the boiler evaporates leaving the salts dissolved in the water behind which means the salt concentration in the remaining boiler water increases. To avoid exceeding the permissible salt concentration, salt must continuously be removed and this is accompanied by energy and water losses.
To reduce the surface blowdown rate, demineralisation of the freshwater is advisable, especially with low condensate accumulation rates <50% and high conductivity in the freshwater. Demineralisation takes place after softening. One of the most common methods is reverse osmosis.
Calculation of surface blowdown rate
The required surface blowdown rate can be calculated based on the conductivity measured in the feed water or the make-up water parameters and condensate accumulation rate (the conductivity of condensate is normally negligible):
In addition to conductivity, the surface blowdown rate is determined by other water parameters such as the silicic acid content SiO2 or (carbonate) hardness with the limit value 8.2. In this case the biggest value calculated is always decisive for the actual surface blowdown rate.
These parameters can be calculated along the same lines as the above formula for the conductivity:
Unit |
Conductivity |
SiO2 |
Acid capacity 8.2 |
|
Steam quantity |
[kg/h] |
10,000 |
10,000 |
10,000 |
Surface blowdown rate (as a function of steam quantity)1) |
[%] |
3.27 |
2.56 |
3.00 |
Proportion of condensate c |
[%] |
50 |
50 |
50 |
Proportion of freshwater |
[%] |
50 |
50 |
50 |
Value in freshwater |
[µS/cm] |
380 |
7.5 [mg/l] |
0.7 [mmol/l] |
Limit, boiler water |
[µS/cm] |
6,000 |
150 [mg/l] |
12 [mmol/l] |
Value in feed water |
[µS/cm] |
190 |
3.75 |
0.35 |
Surface blowdown quantity |
[kg/h] |
327 |
256 |
300 |
Feed water quantity |
[kg/h] |
10,327 |
10,256 |
10,300 |
Calculation of surface blowdown rate
1) The surface blowdown rate is determined by the biggest value. In this example, the value for conductivity 3.27%.
Reverse osmosis
Reverse osmosis is based on the principle that the diffusion resistance of the pores of the separation membranes is significantly lower for the smaller water molecules than the resistance of the bigger ions dissolved in the water. If the system is in equilibrium, the pressure on the concentrate side (retentate) is higher than the pressure on the pure water side (permeate). This is also referred to as osmotic pressure and is apparent from a difference in height.
Demineralisation of the water for technical operations is carried out with the assistance of artificial membranes whereby the natural osmosis process is reversed by means of pressure charging on the concentrate side. Dissolved salts and also organic substances are more or less completely retained during this process.
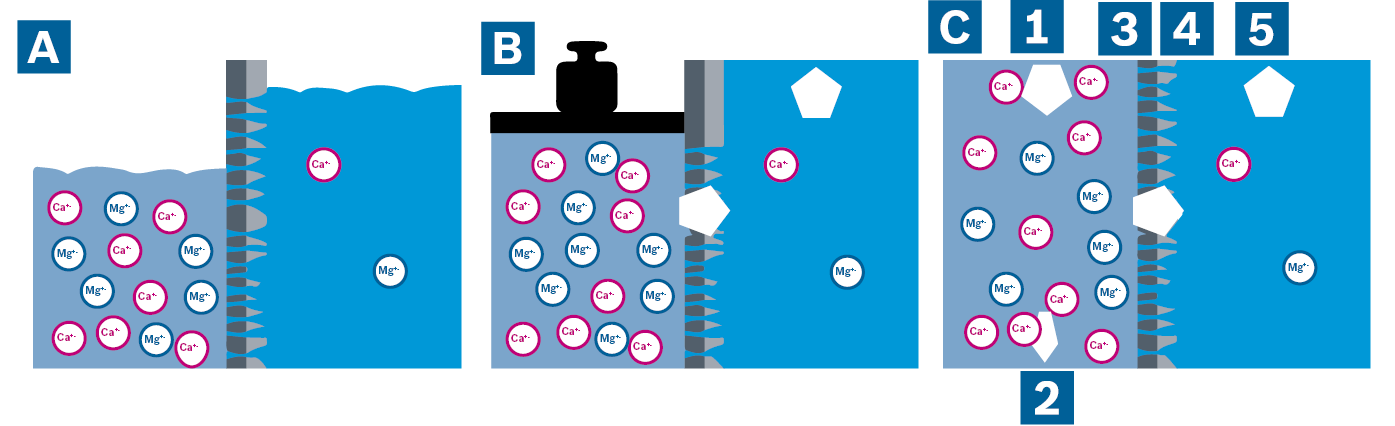
Visualisation of osmotic pressure (A), reverse osmosis by pressure charging on the concentrate side (B) and the continuous reverse osmosis process (C)
|
Illustration of osmotic pressure |
|
Retentate |
|
|
Reverse osmosis by pressure charging on the concentrate side |
|
Semi-permeable membrane |
|
|
Process of continuous reverse osmosis |
|
Carrier layer |
|
|
Freshwater |
|
Permeate |
Separation process |
Strainer filtration |
Fine filtration |
Particle filtration |
Micro filtration |
Ultra filtration (UF) |
Nano filtration (NF) |
Reverse osmosis (RO) |
Separation limits |
> 500 µm |
5 – 500 µm |
1 – 10 µm |
0.1 – 1 µm |
0.01 – 0.1 µm |
0.001 – 0.01 µm |
< 0.001 µm |
Separable substances |
Grains, |
Larger |
Small |
Microparticles, germs, bacteria, viruses |
Viruses and molecular substances |
Low-molecular substances and humic substances |
Ions |
Procedure in water technology |
Screening, cyclones, sedimentation, clarification |
Fabric filter, cloth filter |
Multi-layer fast filter, membrane filtration (MF) |
Multi-layer slow filter, membrane filtration (MF) |
Membrane filtration (UF) |
Membrane filtration (NF) |
Reverse osmosis (RO) |
Separation limits |
![]() |
General overview of separation limits and separation methods in water treatment
The generated pure water is continuously available and the condensate that accumulates can be introduced into the sewer system without further treatment.
The prerequisite for using a reverse osmosis system is that the water is softened beforehand. The water must also be clear and free of insoluble foreign matter and it is especially important that it is also free of organic contaminants to avoid blocking the membranes.
The softened water is admitted to the modules which are equipped with a membrane at a pressure of < 40 bar. Fine water and a very small proportion of small salt ions diffuse through the membrane and form the permeate (latin: permeare = penetrate), which is then available as partially demineralised water. The proportion of permeate in the filtered water is 80 – 95%. The rest (5 – 20%) of the original volume of water is the salty concentrate, also referred to as retentate (latin: retinere = retain), which is discarded.
The reverse osmosis process takes place while the system is continuously in operation, is virtually chemical-free and removes roughly 98% of the salts so that the conductivity of the permeate is less than 15 μS/cm. The system is monitored throughout this process to make sure it is functioning correctly by measuring the conductivity in the permeate.
In order to keep the systems that perform the reverse osmosis as small as possible, a permeate collection vessel is recommended. This then feeds the deaerator of the feed water vessel.
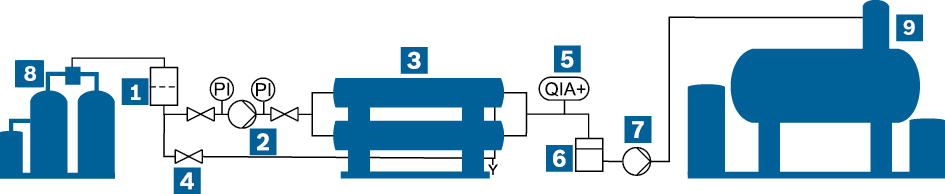
Schematic representation of a reverse osmosis water treatment with permeate vessel
|
Filter |
|
Bypass |
|
Permeate pump |
||
|
High-pressure pump |
|
Conductivity monitoring (QIA+) |
|
Water treatment module WTM |
||
|
Reverse osmosis module |
|
Permeate vessel |
|
Water service module WSM-V |
Complete demineralisation
Complete demineralisation of the water with a conductivity of < 0.2 μS/cm is achieved by a complete ion exchange with CO2 percolator, providing a mixed-bed filter is also installed downstream of the anion exchanger. Cation and anion exchangers are combined in the filter. To optimise the complete demineralisation process and reduce consumption of regeneration agent, weak acidic and weak alkaline anion exchangers are installed upstream of the strongly acidic or strongly alkaline exchangers. The completely demineralised water is also referred to as deionised water.
Thermal deaeration
Corrosive components in the feed water or condensate can damage the feed water vessel, boiler, economiser or the pipework. This is mainly caused by oxidisation or carbonic acid corrosion.
Oxidisation causes pinholes to form at various locations in the base material. Over time the material becomes more deeply eroded. “Pitting corrosion”, a typical pattern of damage, appears.

Damage due to oxidation in the boiler and on the pipework
The outward sign of carbonic acid corrosion (CO2 corrosion) on the other hand is almost always a relatively uniform surface erosion of the material.
Thermal deaeration is an effective way to keep oxygen and carbon dioxide levels in the feed water permanently below the harmful range. This method makes use of the fact that gases become less soluble in water as its temperature increases. Their solubility falls to virtually zero at 100°C.
The values are based on the equilibrium of the solubility. In order to actually achieve the outgassing, there must be an active exchange between the gases dissolved in the water and the steam space of the feed water vessel which is achieved using trickle or spray deaerators. Here, a large phase limit is generated to facilitate fast transportation of the material into the gas phase. Furthermore, the water must remain in the container for a certain amount of time in order to expel the remaining gases.
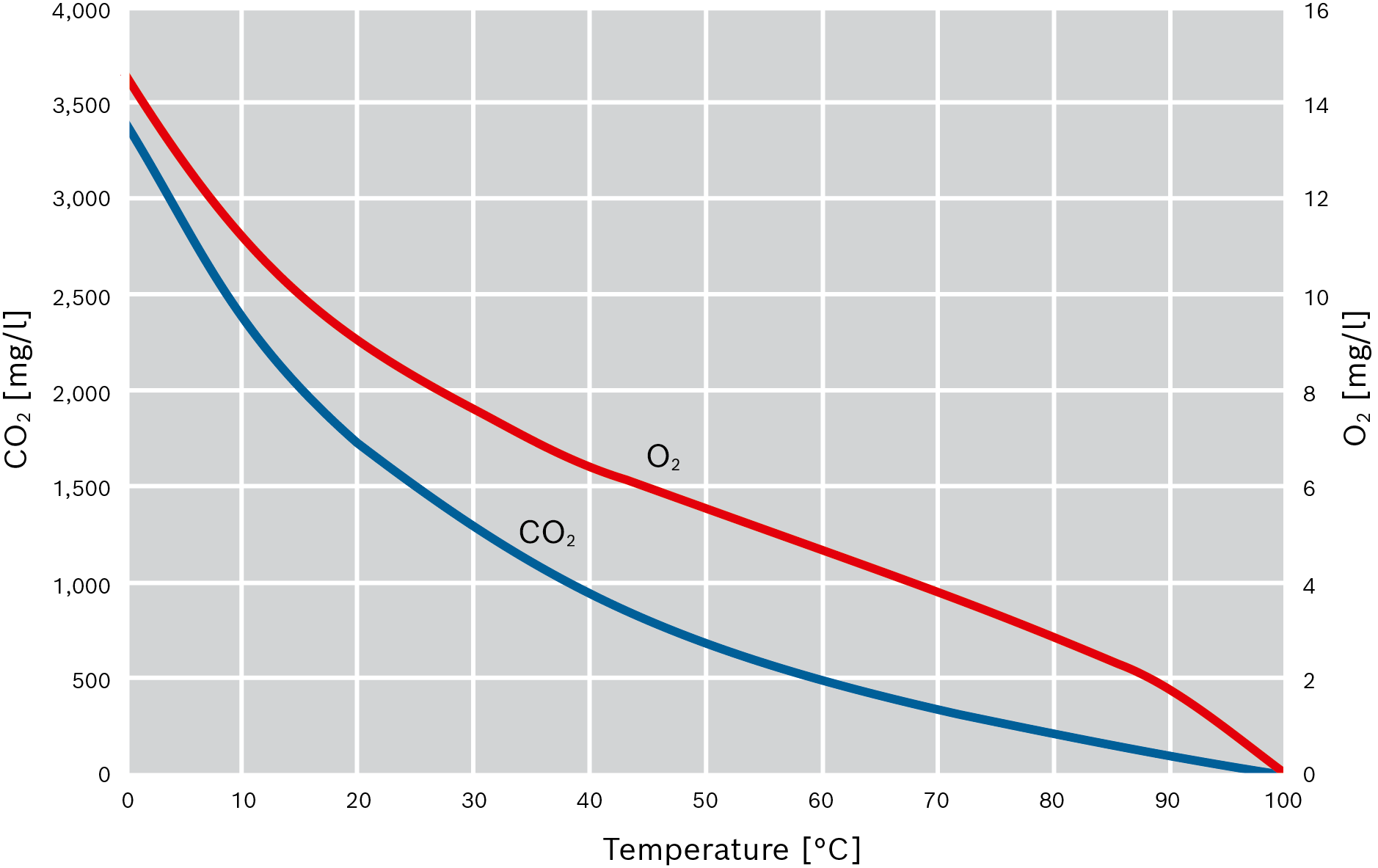
Solubility of oxygen and carbon dioxide in water
|
Carbon dioxide (CO2) |
|
Oxygen (O2) |
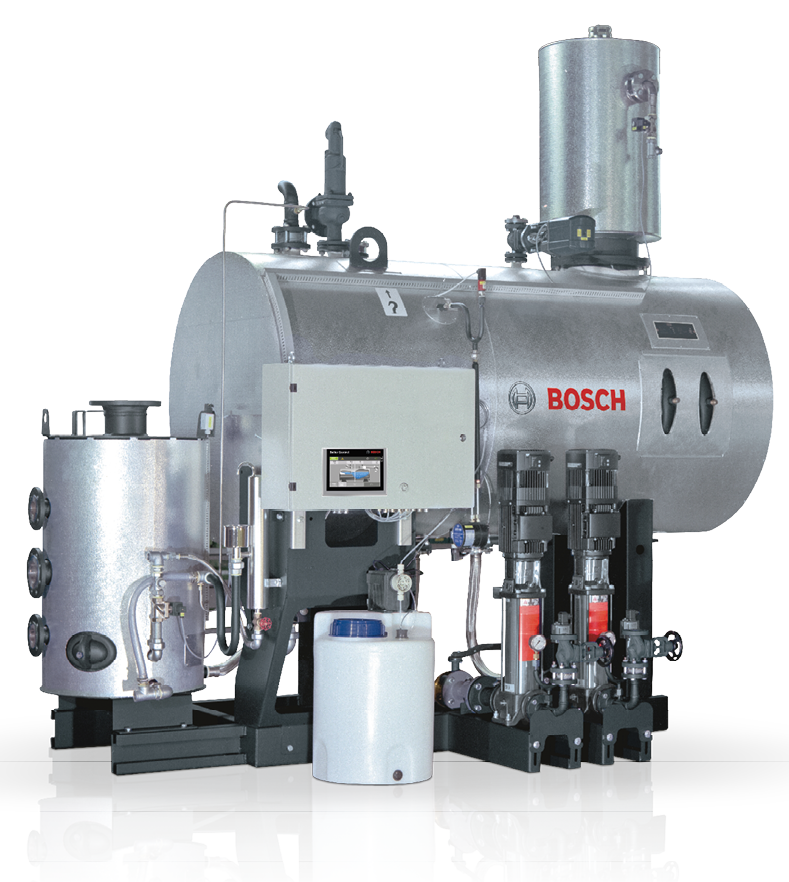
A water service module, consisting of feed water vessel with trickle deaerator, feed pump modules, blowdown expansion vessel, dosing tanks and corresponding control cabinet
Freshwater or oxygenic condensate is introduced at the top in the deaerator dome and finely distributed, either by spray nozzles or trickle trays. It is heated up to boiling temperature by heat-up steam which flows through the deaerator in the countercurrent direction from the bottom to the top. The gases released during heat-up are removed together with the necessary exhaust vapours at the top end of the deaeration dome.
The majority of heat in the exhaust vapour can be transferred to the make-up water via an exhaust vapour heat exchanger (VC) and is therefore retained by the steam system.
Full deaeration
Full deaeration occurs when the maximum oxygen content of 0.02mg O2/l and maximum CO2 content of 1mg CO2/l can be reliably maintained at operating pressures of 0.1 – 0.3 bar and therefore temperatures above 100°C.
Chemical oxygen binders are only used to a very limited extent in this case to ensure the feed water contains no oxygen whatsoever.
Spray deaerator |
Trickle deaerator |
|
Room height |
++ Very compact |
– Deaerating dome extends upwards |
Investment costs |
+ Slightly lower |
– Slightly higher |
Operating conditions deviate from design conditions |
– Partial load barely possible |
++ Very good partial load behaviour |
Use of make-up water continuous control1) |
– Partial load barely possible |
++ Very good partial load behaviour |
Comparison between spray deaerator and trickle deaerator
1) Recommended for heat recovery with make-up water
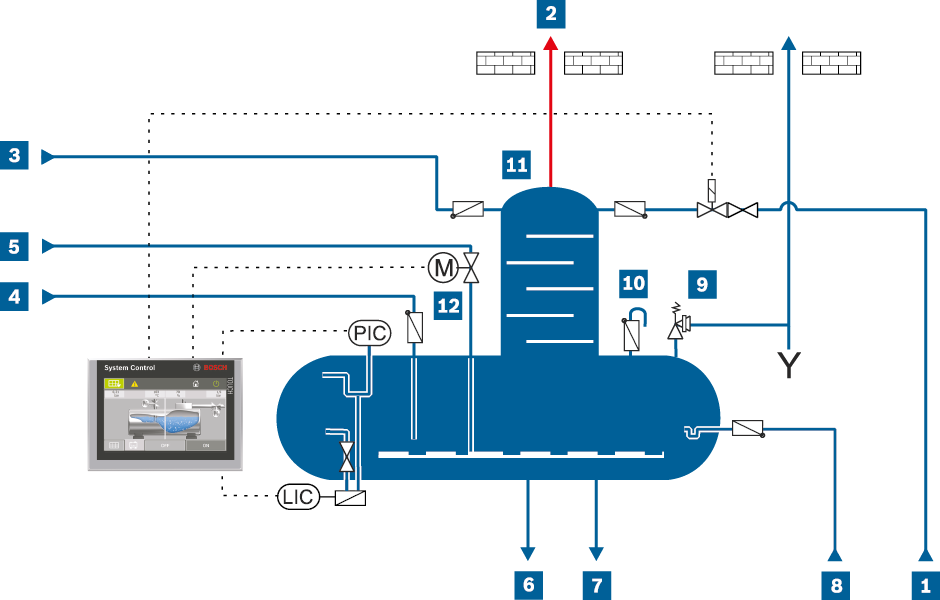
Piping and instrumentation flow diagram for full deaeration with trickle deaerator
LIC |
Level transmitter |
PIC |
Pressure transmitter |
|
Make-up water |
|
Heat-up steam |
|
Safety valve |
||
|
Exhaust vapour |
|
Feed water |
|
Anti-vacuum valve |
||
|
Oxygenic condensate |
|
Drain |
|
Trickle deaerator |
||
|
Oxygen-free condensate |
|
Dosing |
|
Heat-up steam control valve |
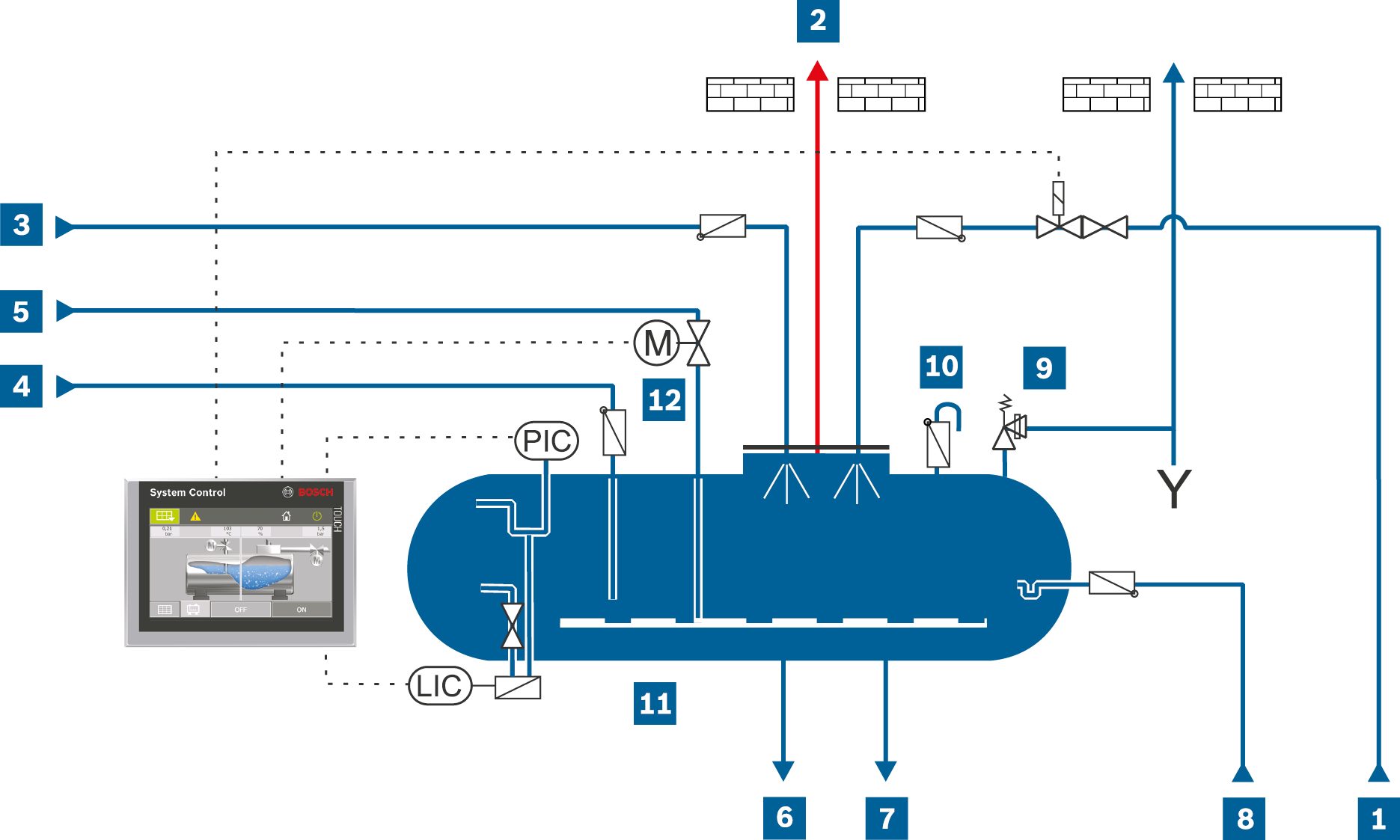
Piping and instrumentation flow diagram for full deaeration with spray deaerator
LIC |
Level transmitter |
PIC |
Pressure transmitter |
|
Make-up water |
|
Heat-up steam |
|
Safety valve |
||
|
Exhaust vapour |
|
Feed water |
|
Anti-vacuum valve |
||
|
Oxygenic condensate |
|
Drain |
|
Spray deaerator |
||
|
Oxygen-free condensate |
|
Dosing |
|
Heat-up steam control valve |
Partial deaeration
If the deaeration only takes place at around 90°C, this is referred to as partial deaeration as a residual quantity of the bonded gases can still remain in the water. In this case, use of chemical oxygen binders must be intensified in order first and foremost to chemically bind the remaining oxygen in the feed water to prevent corrosion in the boiler and rest of the steam system.

Feed water supply – partial deaeration
LI |
Level indicator |
LIC |
Level regulator |
TIC |
Temperature controller |
|
Heat-up steam pipe |
|
Chemical dosing |
|
Control system |
||
|
Condensate feed line |
|
Drain line and overflow |
|
Feed water vessel |
||
|
Exhaust vapour pipe |
|
Feed pump bypass |
||||
|
Make-up water |
|
Feed water line |
Chemical dosing
To make absolutely sure the required water qualities are achieved and monitored, additional treatment must be carried out to improve specific feed water and boiler water characteristics.
This chemical dosing helps ensure the following:
- Binding of residual oxygen
- Reduction of corrosion by setting the pH value
- Stabilisation of residual hardness
- Prevention of deposits and limescale formation
This involves adding the dosing agents to the feed water vessel so that a sufficient reaction time of roughly 30min is achieved.
Sodium sulphite is normally used as an oxygen scavenger agent and trinatrium phosphate is used to bind the residual hardness and raise the pH value.
Technical report: modern water treatment and water analysis