Monitoring of the water quality
Water hardness/limescale
In addition to other harmful ingredients, freshwater also contains alkaline earths, often referred to as “hardness”. We are also familiar with this from the deposits in the kettle or the coffee machine. A limescale layer of only 1mm can significantly reduce heat transfer on the water side. This can lead to significant damage, particularly to components that are subject to high thermal stresses such as the flame tube or the tube plate of the internal reversing chamber.
In this case, the existing softening system has been consistently overloaded by additional in-plant consumers. There was no hardness monitoring and the overloading was therefore not detected.
As a result, residual hardness also ended up in the boiler in which layers had formed on the water side. These layers reduced the heat transfer which in turn caused local overheating and cracks in the tube plate between the holes.
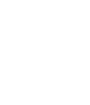
Did you know? With a water hardness of 10° dH (medium hardness), up to 70g of limescale is transported per m3 of water. If this value is extrapolated for a boiler with a steam output of 10 t/h operating continuously for 10 days, the results is nearly 500kg of limescale in the boiler. |
Damage: |
|
Cause: |
|
Remedy: |
|
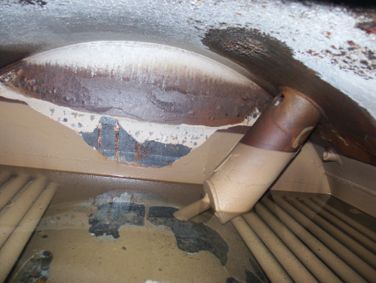
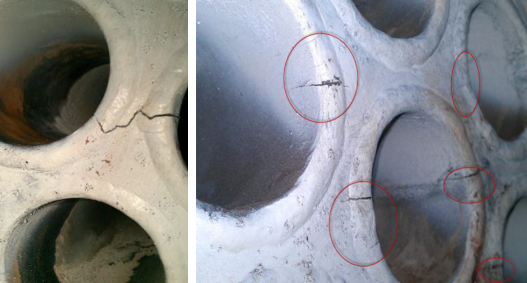
Ingress of foreign matter into condensate
From an energy and efficiency standpoint it makes sense to return condensate that accumulates during operation to the water/steam circuit. It can however become contaminated during the production process. In this example, the condensate has been contaminated with grease due to a leaking production heat exchanger. The grease was deposited in the boiler on the heating surfaces and also on the low-water indicator which caused the heating surfaces to overheat.
Damage: |
|
Cause: |
|
Remedy: |
|