Combustion setting
In addition to the water treatment, the settings of the combustion system are decisive for ensuring economic operation and a long service life of the boiler. These settings should therefore be regularly checked as part of routine maintenance. This should not only involve checking that the boiler is working correctly but also that actual operation corresponds to the planned operation.
Burner cycles
The problem of frequent burner cycling is encountered time and again. This can have many different causes, such as oversized design, reduction in demand, changes to operating conditions and also insufficient control settings.
The rule that generally applies for all systems is that burner cycling should be avoided whenever possible. During pre-ventilation, cold air is routed through the boiler. This leads to higher thermal stresses and therefore a reduced service life and greater heat losses. Cycling can often be significantly reduced simply by optimising the settings of the load control.
If the burner is far too big for the required steam output, it will need to be replaced.
Technical report: avoidable stresses at steam shell boilers
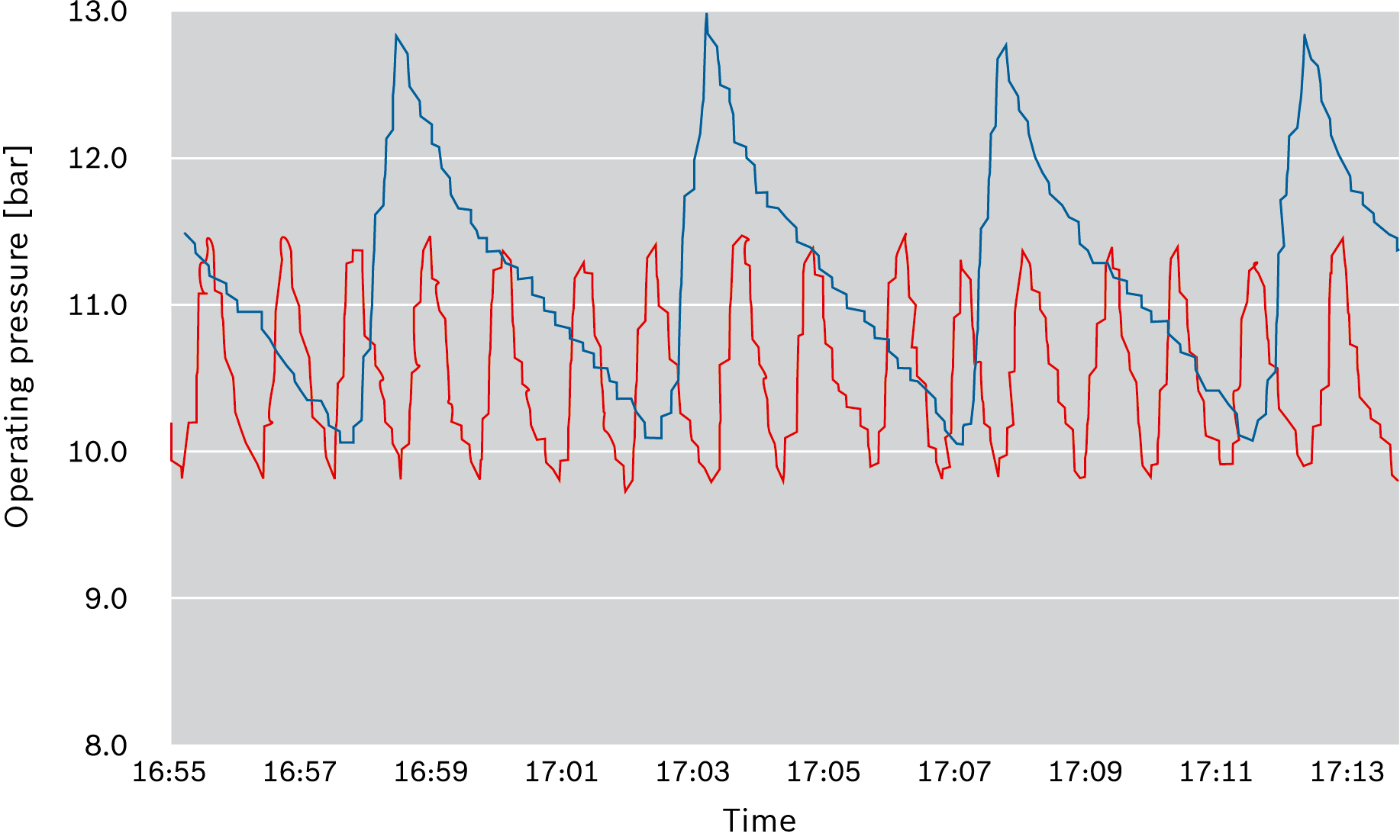
Reduction of burner cycling via optimised setting
|
Burner cycling in minute range |
|
Burner cycling following readjustment of the control range |
Problem: |
|
Cause: |
|
Remedy: |
|
Boiler overload
The design of shell boilers makes them relatively insensitive to load fluctuations of the consumers. A short-term increase in steam feed of up to 20% over the design capacity which can arise due to a pressure drop in the boiler usually does not pose a problem. If the load demand is higher, this can lead to significant problems in the system and boiler and to strong fluctuations of the water level in the boiler. Water carried from the boiler into the system can lead to extremely high steam moisture content that causes steam hammer.
Problem: |
|
Cause: |
|
Remedy: |
|