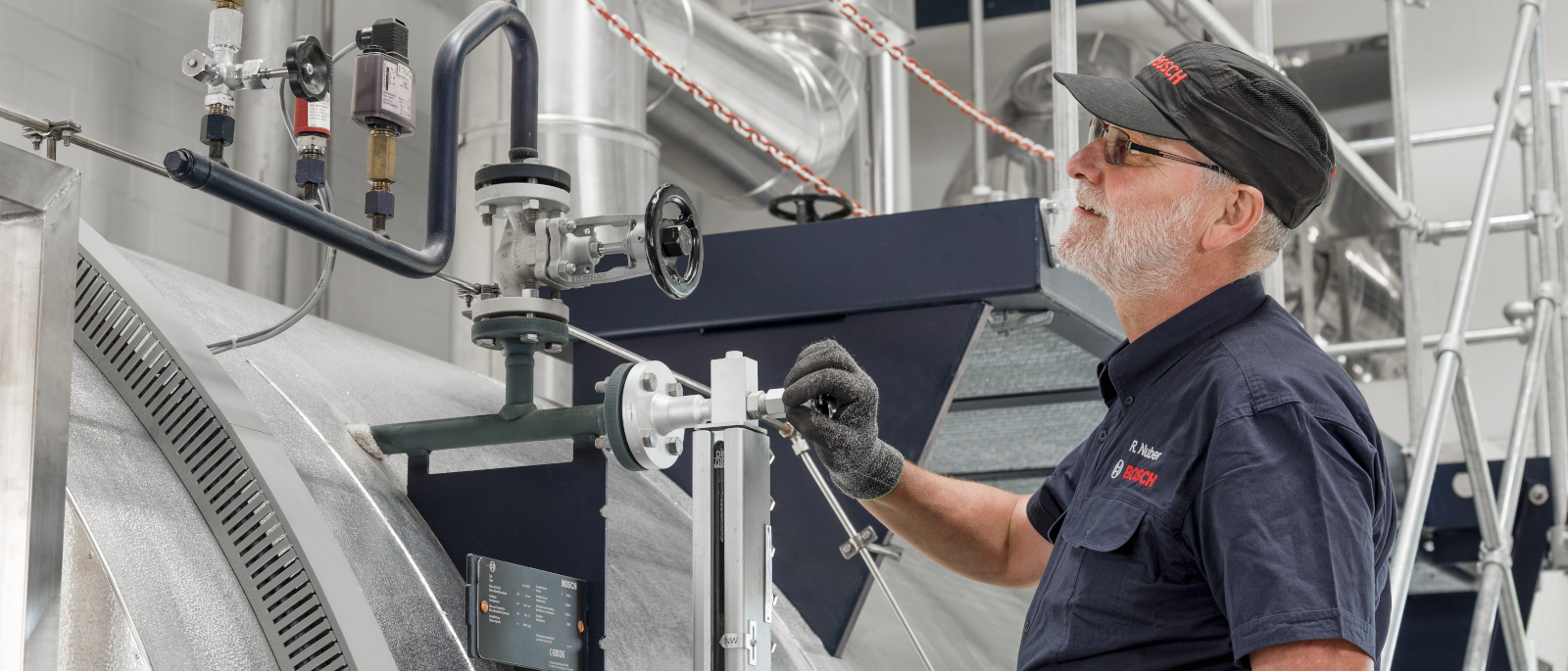
During installation
Installation and assembly errors occur now and again because in larger projects, several companies are often working together for the first time. Many interfaces and many installation instructions of specific manufacturers must be observed. Time pressure which is often an aspect of such projects can also have a decisive effect. The various trades install their pipework without coordinating with one another and whoever arrives on-site first installs first without taking the following installations into account.
In these situations problematic faults occur, e.g. a volumeter installed in the incorrect flow direction or incorrect connections at a heat exchanger or at safety valves which come to attention during commissioning and must then be rectified.
Unfortunately, often systems and pipework are either poorly or not perfectly installed. The following problems are either not or only partially identified during commissioning and acceptance of the system, which then leads to a permanent deterioration in operating conditions.
Signs of this are:
- Overly high investment costs (too many elbows, nor direct pipe routing)
- Corresponding operating costs (high-pressure losses, high heat losses)
- Poor operability and maintenance options
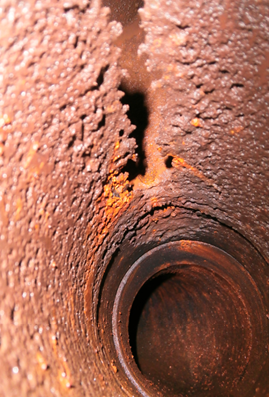
Pipe routing
For various reasons, the pipework must be routed through changes in height at many points. In these situations, two simple basic rules should be followed.
- Drain pipework at the lowest point
- Vent the pipework at the highest point
Steam pipes
When starting up, it is especially important to bear in mind that large amounts of condensate accumulate in steam pipes, not only during the heat-up operation but also during continuous operation due to the heat losses in the pipework. This condensate must be removed from the steam pipe as otherwise water droplets could form and be carried along at high speed in the steam flow which leads to water hammer resulting in damage to the pipework, valves or holders. The following points must be observed when routing the steam pipe.
Provide dewatering points
- Immediate upstream of all control valves and pressure reducers to prevent condensate accumulating when these fittings are closed
- Upstream of manual or motorised valves that remain closed for longer periods
- At the lowest points in all vertical sections of pipework and before changes in height
- At the end of the pipe
Observe pipe gradients
It must be possible for condensate that accumulates in a section of pipework to flow to the nearest condensate drain. In the flow direction, this is supported by the prevailing flow speed in the pipe. A gradient in the flow direction is therefore desirable. There should be a dewatering point every 25 – 50m.
The gradient should not be less than 1 – 3%, and should ideally increase slightly the greater the distance from the last drainage point as a larger quantity of condensate must then also be carried along.
Short pipe sections can also be dewatered in the counterflow direction by increasing the gradient accordingly to >5%.
The important thing is to ensure that the condensate can flow away unimpeded and that water pockets cannot form at any point in the pipework.
Condensate collector pipes
Due to the high-pressure gradient, only a small connection diameter (DN 15 – 25) is required at the end of the condensate drains for dewatering of the pipework. However, if the diameter of the connection end that connects directly to the steam pipe is too small, some of the condensate flowing at high speed through the pipework is flushed beyond the dewatering point which renders the condensate drain more or less ineffective. The condensate collector pipe should therefore always be sufficiently sized to ensure effective dewatering. It must also be ensured that sufficient volume is available in the condensate collector pipe for dirt deposits to minimise failures of the condensate drains.
The collector pipe also acts as a storage volume, particularly when starting up the system when large condensate accumulation rates occur due to heating of the pipework. The connection of the condensate drain should branch off roughly 50 – 100mm above the base of the collecting pipe to prevent dirt and deposits directly entering the drain.
Problems: |
|
Cause: |
|
Remedy: |
|
Merging of pipework
Merging of pipework with the same function is a standard procedure in plant engineering. It goes without saying that steam pipes from several boiler systems are combined into one supply pipe with suitable nominal diameter, for example. However, this is only possible if the function is not impaired. This can lead to severe problems, particularly in the case of safety valve blow-off pipes.
Safety valve blow-off pipes must always be routed separately to the open air and, whenever possible, via the most direct route. When pipework is merged, this affects the function of the safety valve and the necessary blow-off quantities are undercut. As the reaction forces that occur when the valve responds are high, the pipe could even break off.
Problems: |
|
Cause: |
|
Remedy: |
|
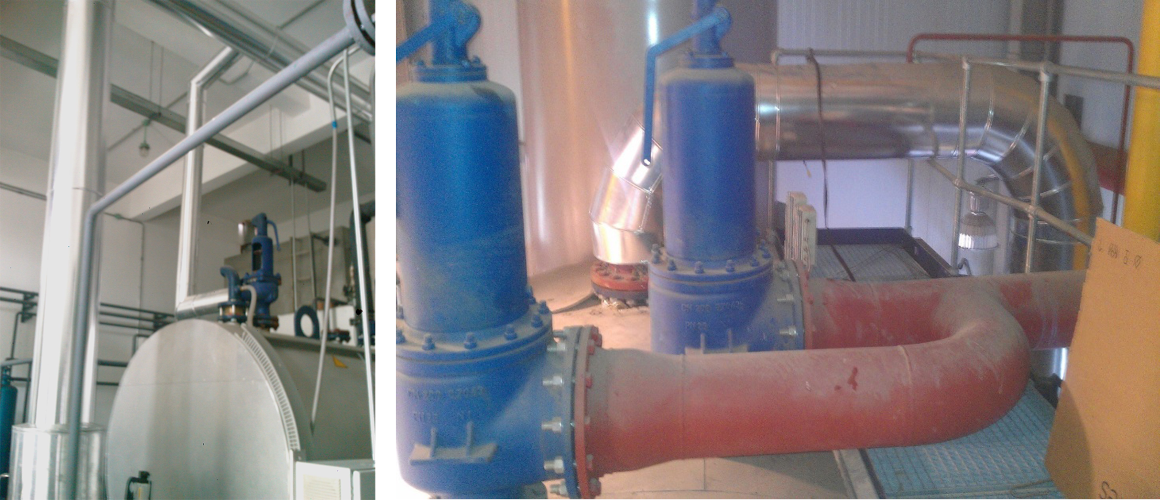
Impermissible merging of safety valve and expansion steam pipe
Reduction of internal diameter and excessively long pipework
Air vent lines
If air vent lines, such as those used on the bottom blowdown expansion vessel are not routed onwards with the same nominal diameter as specified, there is a risk of an impermissible build-up of pressure. This occurs as a consequence of restricted air flow and can lead to destruction of the vessel which is designed for unpressurised operation (≤ 0.5 bar).
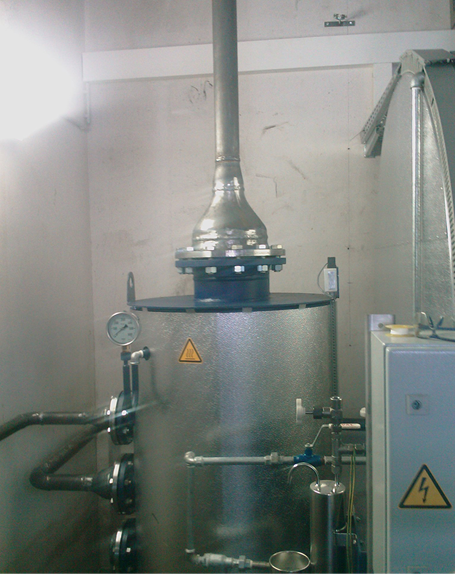
Exhaust vapour pipe
If the internal diameter of the exhaust vapour pipe from the deaerator is reduced, this can impair the removal of oxygen and carbon dioxide to such an extrem, meaning that full deaeration can no longer take place. This would lead to corrosion in the boiler and the pipework. If in addition the water quality is not regularly tested as prescribed, large components of the boiler system may need to be replaced.
Problems: |
|
Cause: |
|
Remedy: |
|
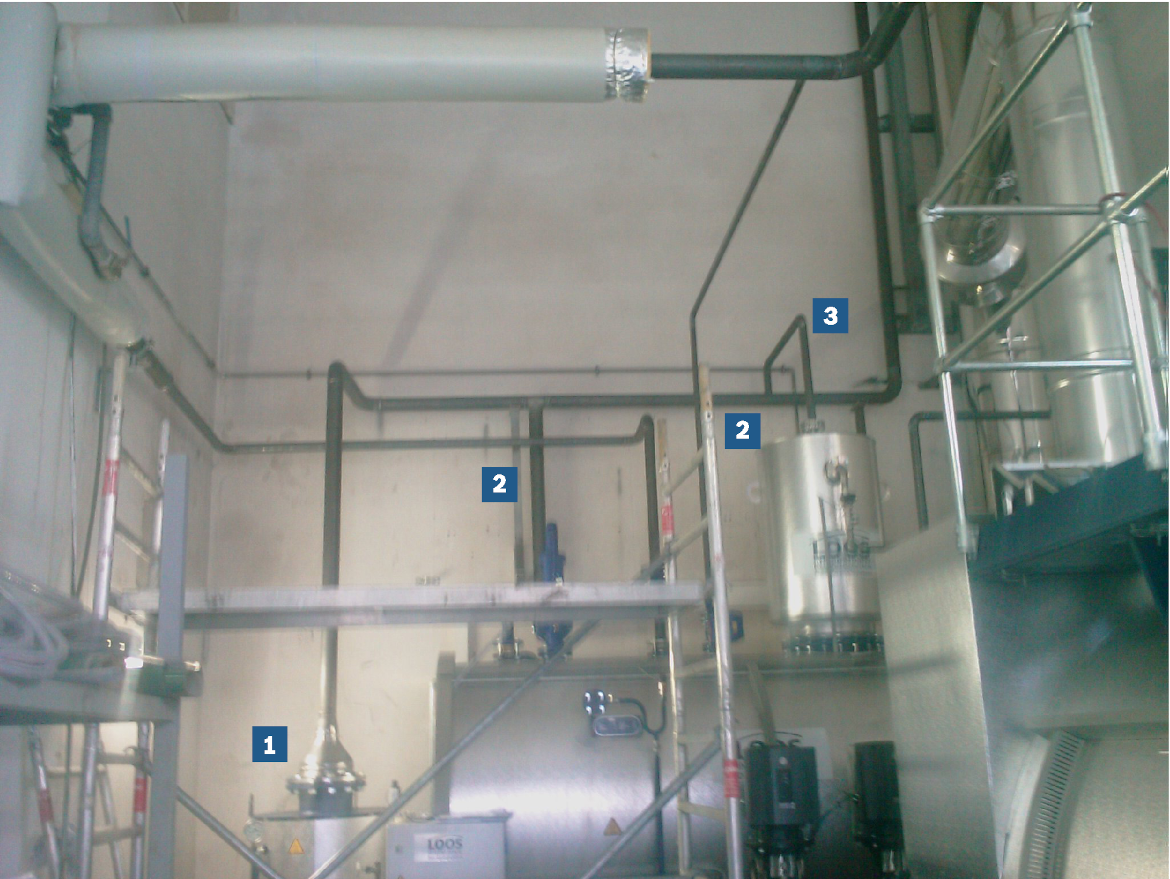
Hazard free outlet
All pipework, especially safety valve blow-off pipes that divert steam to the open air, must be routed in such a manner that they do not pose any further danger to persons, systems or the building. The steam normally flows at a very high speed and high temperature to the open air. The outlet must therefore not cross any routes nor should it be directed at temperature-sensitive parts of the system.
Damage: |
|
Cause: |
|
Remedy: |
|
![]() |
Safety valve blow-off pipe
Incorrectly installed valves
Valves are often fitted incorrectly in the flow direction. As the function is impaired this is normally discovered immediately. This cannot always be detected immediately, especially in the case of non-return valves. In this case the non-return valve was incorrectly installed at the feed water control module bypass which meant that the minimum quantity required for the pump could no longer flow back to the feed water vessel. This initially led to cavitation in the first feed water pump. The cause was not investigated further as the feed water pump was replaced under guarantee. As the fault was not rectified, cavitation occurred in the second and third pump. Only then was the actual cause investigated and subsequently rectified.
Damage: |
|
Cause: |
|
Remedy: |
|
Support
Now and again, serious defects are found on pipework holders, such as:
- Insufficient sizing of holders
- Distances between holders too large
- Thermal expansion during operation not taken into consideration
- Wall or ceiling too weak to absorb the forces
The forces released when the safety valve responds cannot be absorbed either by the safety valve or the metal roof. Here, the discharge pipes are propping each other up, which does not help the situation. Fortunately the fault was discovered before the initial test as otherwise there would have been a risk of the pipework rupturing.
Problem: |
|
Cause: |
|
Remedy: |
|