Control
Optimising and adjusting the control of boiler systems to the actual operation also represents a huge potential for savings. This optimisation always makes sense as the design conditions of boiler systems are different to the actual operating conditions. This may become necessary if additional consumers are subsequently installed in new systems, for example, or if current operations change as a result of converting and extending production with existing systems.
Reduction of operating pressure
An average operating pressure based on the required temperature level and pressure losses to the consumers are defined at the concept and design stages of a steam boiler system. However, this design is frequently based on a very conservative estimate, when in fact a slightly lower operating pressure would be sufficient during operation in practise.
For the purpose of energetic optimisation during operation, it therefore makes sense to determine the necessary average operating pressure and set this at the boiler control. Due to the reduction in operating pressure, the temperature in the boiler and steam pipes falls which reduces radiation and conduction losses.
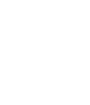
With each change of the operating pressure, the conditions at the system must be taken into account. |
Info on Average operating pressure
A reduction in the average operating pressure of 8 bar (≙ 175°C saturated steam temperature) to 6 bar (≙ 165°C saturated steam temperature) immediately reduces the conduction and radiation heat losses by 7% which means that fuel savings of around 0.2% can be achieved.
In addition to the heat losses, the flue gas temperature also falls slightly which additionally increases the annual degree of utilisation.
Additionally, the full operating pressure is not always required outside the main operating times of a steam boiler system (e.g. at the weekend). It often makes sense to set a lower operating pressure at these times.
Boiler sequence control
If several steam boilers are installed at a plant, the operation of each single boiler can be optimised by using a boiler sequence control.
The task of a boiler sequence control is to match the number of boilers actually activated to the current power demand. This adjustment can be achieved by automatically switching the lag boilers on or off according to the criteria of the sequence control. This ensures an energy-saving mode of operation of the boiler system. Adjusting the boiler sequence to the actual power demand reduces pre-ventilation losses, automatically carries over boilers into heat maintenance mode and achieves efficiency-optimised operation of boilers. This adjustment and associated reduction in heat losses improves the annual degree of utilisation.