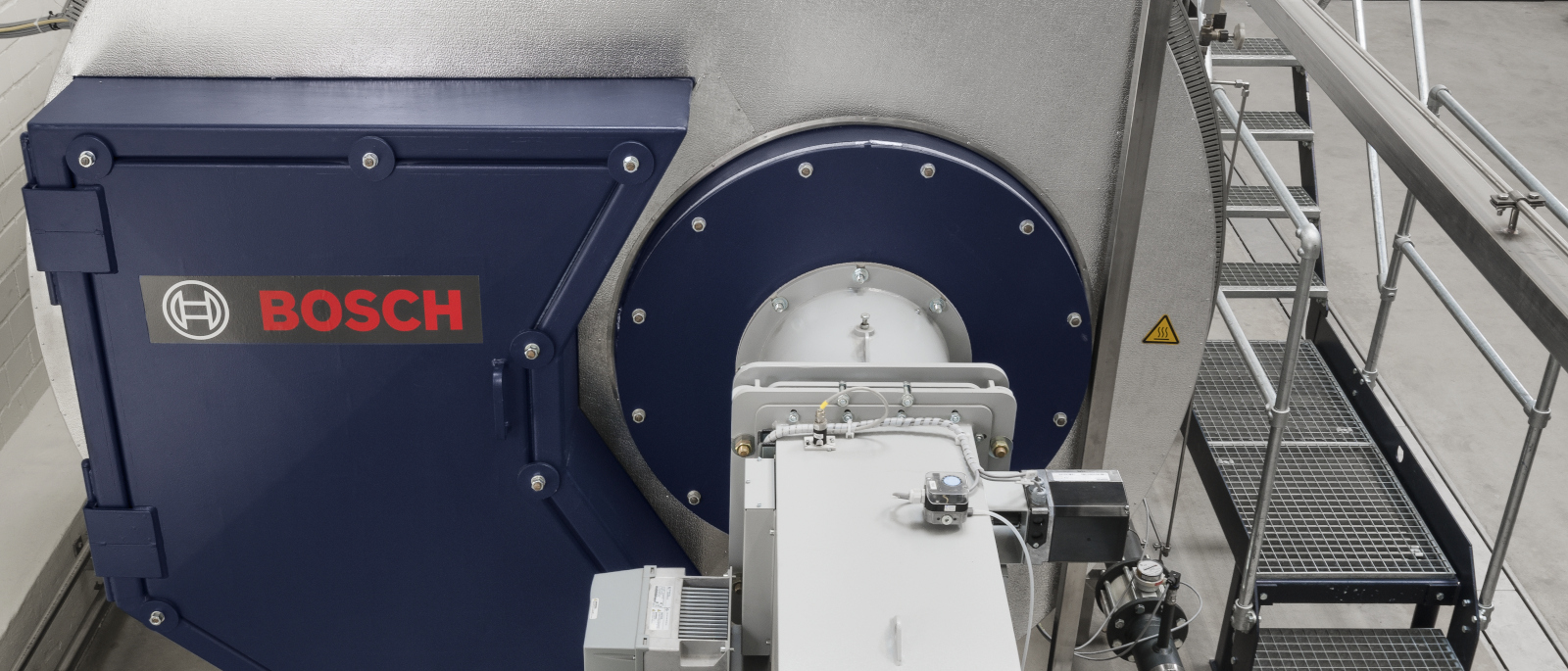
Increasing
combustion efficiency
Flue gas temperature or flue gas loss
Economiser
The flue gas temperatures at the boiler outlet are normally roughly 60K above the temperature of the product inside the steam boiler.
Fig. „Integrated economiser in UL-S“
At an operating pressure of 10 bar, which corresponds to a saturated steam temperature of 185°C, the flue gas temperature is therefore roughly 245°C. This corresponds to a flue gas loss of roughly 11%. As shown in the graphic (Fig. „Efficiency gain for various exemplary sizes of economiser“), the flue gas loss can be reduced by roughly 1 percentage point, or the boiler efficiency increased accordingly, with each 20°C reduction in flue gas temperature.
Using an integrated or downstream economiser, the flue gas temperature can be reduced to 120 – 140°C, depending on the economiser design, which reduces the flue gas loss significantly. During this process, the heat in the flue gases is transferred to the boiler feed water flowing in countercurrent. The heat removed from the flue gas flow is fed to the boiler via the heated feed water. This increases the combustion efficiency by 5 – 7%.
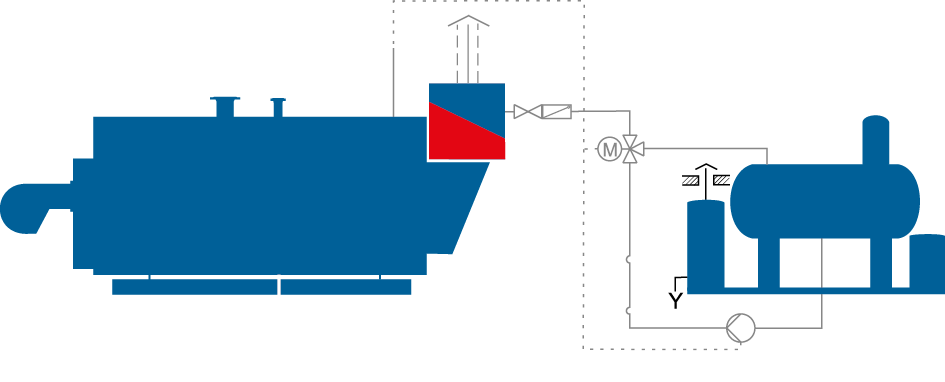
Simplified flow diagram of a steam boiler system with integrated economiser