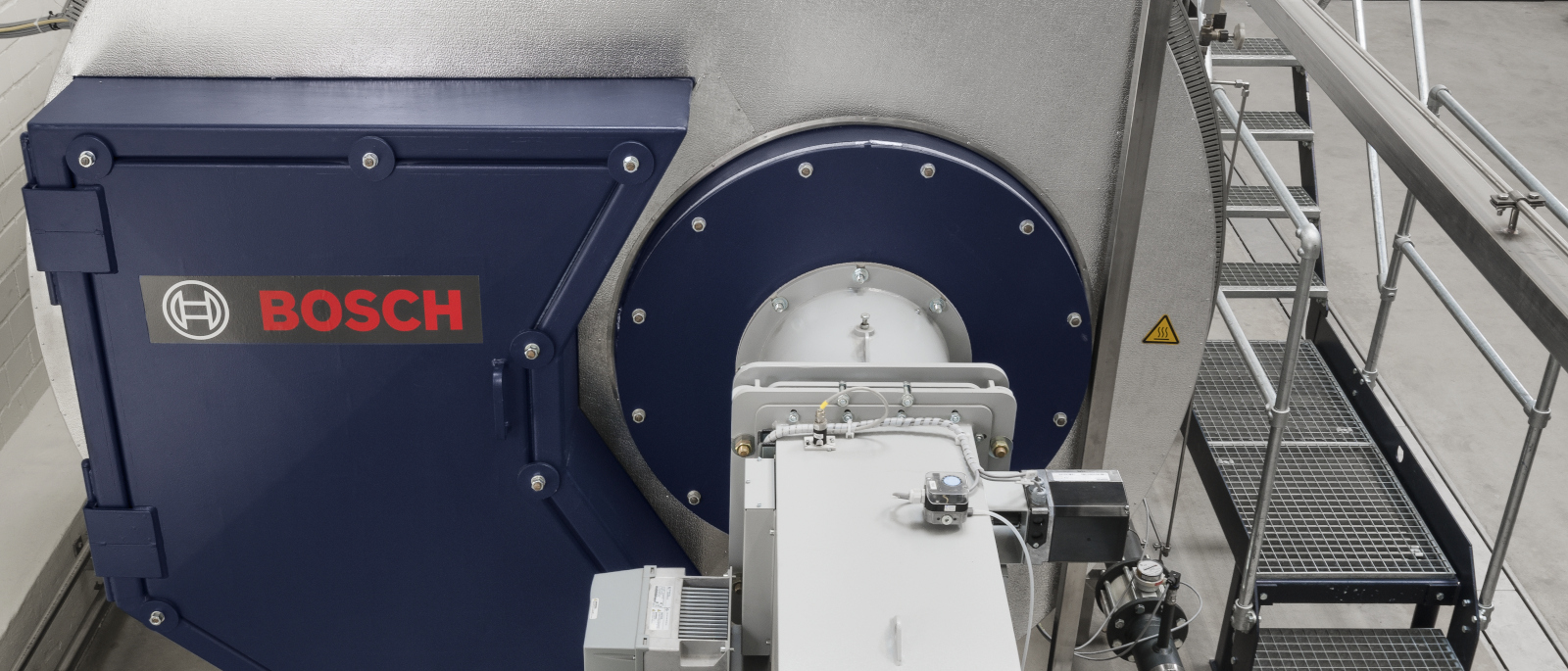
Aumento de la
eficiencia de combustión
Temperatura o pérdida de gases de combustión
Economizador
La temperatura de los gases de combustión a la salida de la caldera suele ser unos 60 K superior a la temperatura del vapor saturado en el interior de la caldera de vapor.
Fig. „Economizador integrado en UL-S“
A una presión de funcionamiento de 10 bares, que corresponde a una temperatura de vapor saturado de 185 °C, la temperatura de los gases de combustión es de aproximadamente 245 °C. Esto corresponde a una pérdida de gases de combustión de aproximadamente el 11 %. Esto corresponde a una pérdida de gases de combustión de aproximadamente el 11 %. Como se muestra en el gráfico (Fig. „Aumento de la eficiencia con economizadores de distintos tamaños“), la pérdida de gases de combustión se puede reducir en aproximadamente 1 punto porcentual, o aumentar el rendimiento de la caldera en consecuencia, con cada reducción de 20 °C en la temperatura de los gases de combustión.
Utilizando un economizador integrado o conectado a continuación, la temperatura de los gases de combustión puede reducirse a 120 – 140°C, dependiendo del diseño del economizador, lo que reduce significativamente la pérdida de gases de combustión. Durante este proceso, el calor de los gases de combustión se transfiere al agua de alimentación de la caldera que fluye en contracorriente. El calor extraído del flujo de gases de combustión se introduce en la caldera a través del agua de alimentación calentada. Esto aumenta el rendimiento de la combustión en un 5 – 7%.
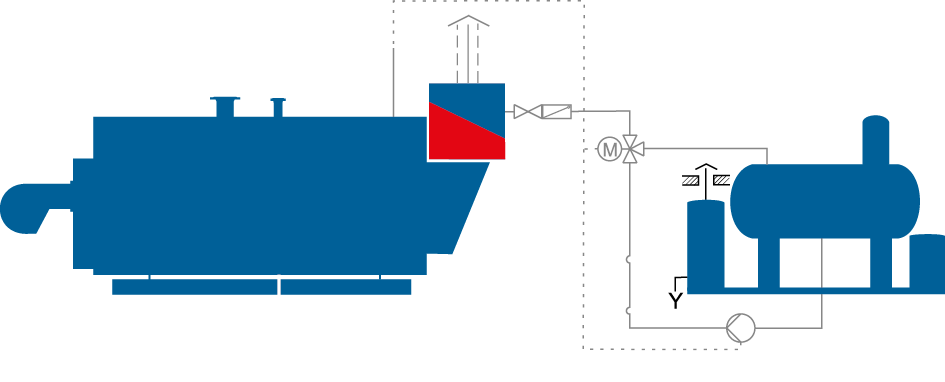
Diagrama de flujo simplificado de un sistema de caldera de vapor con economizador integrado