Consumption analysis
If the nominal design steam quantity is known, the planning must include a step for defining the steam output of the individual boilers in the system. The aim of this is to determine the maximum steam demand arising during operation, as well as the minimum steam demand. Any design safety margins or expansion of the boiler system must also be taken into consideration.
Maximum steam output
The maximum load or nominal load corresponds to the total number of individual consumers that could be in operation at the same time.
To ensure that the chosen maximum steam output is not too high, a check should be carried out to verify whether all heat consumers are or need to be operating at their maximum output at the same time. This is normally not the case, or can be avoided by in-house processes. The required maximum load can therefore be reduced, for example, so that start-up processes of system components and heat exchangers can be staggered, which completely eliminates or at least reduces problems arising during light load phases due to oversizing of the system.
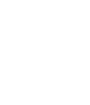
Safety margins during design Of course with the maximum steam output it also makes sense to factor in an appropriate safety margin. To avoid excessive oversizing, the following aspects should be considered when defining the safety margins:
Problems due to oversizing
|
Starting operation
Additional heat is required to bring the system up to operating temperature during the starting operation, especially if the feed water vessel, the pipework or heat exchanger are still cold. The maximum steam output is only available to the consumers once the system is at operating temperature.
Overload
Overloading of individual consumers or the entire system beyond the maximum load of the boiler leads to a very high steam consumption from the boiler. As well as reducing the pressure in the boiler, this also leads to more moisture-laden steam and foaming of the boiler water. Overloading of the boiler should therefore be avoided, e.g. by using pressure reducing stations at the consumers or by protecting the boiler with motorised steam feed valves (SUCcess).
The problem of overloading the steam boiler can also occur when the heat exchangers are correctly configured. The output at the heat exchangers is specified with reference to the design condition and normally includes a reserve of 10 – 30% for the heating surfaces within the heat exchanger. If the heat exchangers are new, they also achieve a higher output when the steam demand is higher.
Development of steam consumption during changes in operation
Special attention should be paid to possible future changes in an operation. If extensions are already planned or envisaged, this must be taken into account in the anticipated maximum steam output. In this case, it is normally possible to devise an overall system concept which allows a degree of flexibility in terms of steam output in order to accommodate subsequent expansion and avoid adversely affecting the current operation due to excessive oversizing.
Minimum output and light load phases
The minimum output normally occurs when production stops at night or at the weekend. In addition to the internal consumers, so-called downtime losses in particular must be taken into account. They do not depend on the current steam demand of the system and occur at any time.
These are essentially:
- Heat losses due to heat emission at the steam boiler
- Heat losses in pipework
- Heat losses at the components
- Exhaust vapour losses at the deaerating unit
Light load phases during which the required steam output is below the control range of the burner should especially be avoided.
As soon as the burner is cycling frequently (> 4 burner starts/h), efficiency is severely affected due to the occurring pre-ventilation losses.
In addition, the overall service life of the system is impaired by the thermal stresses that occur when the burner starts.
These partial load conditions can often be avoided or reduced by higher level controls and in-house energy management systems, considering they have already been taken into account during the planning of the system.
Technical report: avoidable loads on shell steam boiler systems