Calculation of consumption
When determining the necessary steam output of a steam boiler system, all steam consumers in the steam network must ideally be recorded in a table with their minimum and maximum output and then the output of all consumers must be added up.
In doing so, a distinction should be made between the following consumers:
- Direct consumer (e.g. autoclave)
- Indirect consumer (e.g. heat exchanger)
- Expansion steam losses (e.g. at unpressurised condensate tank)
- Heat losses in the steam pipes
- Own use of boiler system (e.g. heat-up steam for feed water vessel)
Direct consumer
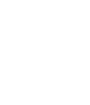
ṁS,dC [kg/h] = quantity of steam for direct consumer |
With direct steam consumers, the steam comes into direct contact with the medium (not via a heat exchanger), where it leaves the system as condensate. The condensate produced is removed with the product (or remains in the product) and is no longer available to the steam circuit. This water consumed must be replaced once again as make-up water by the water treatment system in the steam circuit.
The make-up water must be deaerated by heating it in the feed water vessel. This increases own use required by the steam boiler system.
Direct consumers can, for example, be found in drying processes during humidification, when heating up boiling baths or during sterilisation.
The steam output required at direct steam consumers is stated in the necessary form as mass flow rate ṁS,dC (quantity of steam for direct consumers) in [kg/h]. If a heat output is specified for these steam consumers, the same formulas used with indirect consumers for conversion of thermal output to steam output also apply here.
Indirect consumer
Indirect steam consumers are all types of heat exchanger, in which steam condenses while releasing thermal energy (which heats a medium, e.g. water). The boiling point of the condensate produced during this process initially corresponds to the steam pressure at the inlet to the heat exchanger, but can also be cooled further to below the boiling point, depending on the temperature level of the medium being heated. This is then referred to as supercooled condensate. The condensate is transported via the deaerator back to the feed water vessel.
The thermal output of a heat exchanger is normally specified in [kW] or [MW]. To determine the required steam output in [kg/h] of saturated steam, the thermal output of the heat exchanger must be converted to a saturated steam output.
The saturated steam requirement at a heat exchanger can initially be calculated using the following simple formula:
For a steam pressure of 5 – 18 bar, the difference compared to the actual steam output is <5%. Possible supercooling of the condensate is not taken into account in this case.
To precisely determine the steam output based on the thermal output of a heat exchanger, the evaporation enthalpy must be determined from the saturated steam table with the actual operating pressure of the heat exchanger.
If the condensate produced is supercooled, i.e. to below the boiling point, under all operating conditions the steam output can be calculated using the following formula, taking the thermal output for supercooling of the condensate into account:
Expansion steam losses
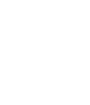
ṁS,ES [kg/h] = quantity of expansion steam |
Expansion steam occurs when hot pressurised condensate expands at the pressure below the boiling pressure. This happens, for example, when condensate flows through condensate drains or valves or when it flows into an open condensate tank at atmospheric pressure. The higher the temperature of the condensate, the more expansion steam is produced.
The quantity of the expansion steam produced can be read off from the diagram or calculated from the water vapour table.
It has to be considered in this case that the quantity of expansion steam may already be reduced due to supercooling of condensate. If the expansion steam is released into the surroundings, the steam lost from the boiler system must be reintroduced as make-up water, along the same lines as when water is lost from direct consumers.
The expansion steam can also be utilised through heat recovery measures and reintroduced directly into the water circuit.
Heat losses in steam pipes
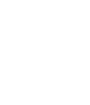
ṁS,lP [kg/h] = quantity of steam for equalisation of heat losses in the steam pipes |
The heat loss in the pipework must also be taken into account in the steam output design. If the pipework is well insulated, a heat energy demand of roughly 10kg steam per hour and in each pipe (10kgS / (h · 100m)) can be assumed.
To calculate heat losses more accurately, a separate calculation must be carried out for every pipe run based on the nominal diameter, length of the pipe and insulation thickness.
The heat losses at valves, flange connections and containers must also be taken into account accordingly. Corresponding guide values can be found in the chapter Efficiency.
Unfortunately the heat loss via poorly or only partially insulated pipework, containers and valves is still underestimated. This is mainly the case because during the service life of the system, the insulation is removed for inspection or maintenance and not reinstalled afterwards. The insulation of pipework (both in the steam and also the condensate system) represents one of the most economical cost-saving measures in existing systems.
If the heat loss in the pipework is precisely calculated, the steam demand for these losses must be determined in the same manner as the heat demand for an indirect consumer.
Own use of steam boiler system
In order to operate, the steam boiler system also requires some of the steam output for its own use. The actual steam output required for own use can only be determined based on in-depth knowledge of the mode of operation of the overall steam boiler system. The heat-up steam quantity for the feed water vessel is decisive for the internal steam consumption.
The heat-up steam at the feed water vessel depends in turn on the condensate return flow from the steam consumers with the relevant condensate temperatures, make-up water demand and water losses from the boiler for surface blowdown and bottom blowdown.
The quantity of steam for own use is required to operate the following heat consumers. To obtain a rough guide value to initially design the necessary steam output, the steam demand for own use can be estimated as follows:
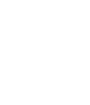
ṁOU [kg/h] = own use of boiler system:
|
Roughly 6 – 16% of the total steam output is therefore required by the boiler for own use.
To precisely calculate the steam required for own use, the precise data for the make-up water demand, type of water treatment and chemical mode of operation of the boiler, condensate return with condensate temperatures and, if necessary, the fuel preheating must be available.
The steam required for own use can however be significantly reduced by heat recovery measures such as exhaust vapour coolers, flash tanks, brine coolers and feed water coolers or condensation economisers and a salt-free mode of operation with osmosis water treatment.
To precisely calculate the quantity of steam required for own use, the following heat-up steam quantities must be calculated. Together they represent the heat-up steam quantity for the feed water vessel.
Heating up make-up water
In order to compensate for the steam losses in the steam circuit, e.g. due to the direct consumers, treated make-up water must be fed into it.
During deaeration, the cold make-up water must be heated from roughly 10°C to 103°C. The required thermal output is obtained as internal steam consumption directly from the steam output of the boiler.
The make-up water demand can therefore be calculated from the steam output, surface blowdown, exhaust vapours and the condensate return flow:
Heat-up of oxygenic condensate
In addition to heating up make-up water, the oxygenic condensate which is collected in open condensate tanks and is therefore colder than 103°C must also be heated back up to feed water temperature. The temperature of oxygenic condensate is frequently between 50 – 90°C.
The required thermal output is obtained as own steam consumption directly from the steam output of the boiler.
Exhaust vapours during deaeration
So the gases such as oxygen and CO2 dissolved in the make-up water and oxygenic condensate can also be removed from the deaerator, a proportion of roughly 0.5% of the mass flow rate consisting of make-up water and oxygenic condensate must be discharged as exhaust vapours to the atmosphere. During this process, the oxygen, nitrogen and expelled carbon dioxide are transported in the exhaust vapours out of the water into the atmosphere.
As a heat recovery measure, the heat in the exhaust vapours can be condensed in an exhaust vapour cooler and accumulated thermal energy used to heat up the make-up water.
Heat-up steam quantity for feed water vessel
The steam required for own use to heat up the feed water vessel can be summarised by the following formula:
Nominal design steam demand of the boiler system
To determine the overall steam demand of the system, all steam consumers must be added up:
Example calculations of mass and energy balances
The simple example below illustrates the mass and energy balances of a steam boiler system with a small number of components.
For the sake of clarity, the comparison is limited to the change in quantity of recirculated condensate and the type of water treatment. The thermal efficiency in all three cases is around 95%.
Example B1 |
Example B2 |
Example B3 |
Steam system consisting mainly of indirect consumers The make-up water is replenished from an osmosis water treatment unit and the boiler has a low salt mode of operation. |
Steam system consisting mainly of direct consumers Just as in example 1, the make-up water is replenished from an osmosis water treatment unit and the boiler therefore has a low salt mode of operation. |
Steam system with direct (60%) and indirect consumers The make-up water is replenished from a water softener unit and the boiler has a saline mode of operation. |
In systems, for example, where the steam is used in heat exchangers but only some of the condensate is returned (e.g. due to very long distances to the consumers). |
In systems, for example, where the steam is only used for direct consumers, such as those used in the manufacturing of animal feed or in autoclaves. Condensate is only recirculated when using pipework drainage systems and a number of ancillary units. |
In systems, for example, where only some of the condensate is or can be returned, such as those with direct consumers used in the beverage industry (bottle cleaning). |
Summary |
||
Very little heat-up steam is required due to the high-quality water treatment and high condensate accumulation rate. This means that almost all of the steam produced by the boiler can be used in the consumers. The specific fuel demand is low. |
Due to the high-quality water treatment, the surface blowdown rate remains very low despite the low quantity of condensate. However, as the quantity of make-up water that must be heated up is very large, the specific fuel demand is significantly higher. |
The higher surface blowdown rate and high heat losses (without surface blowdown heat recovery) in addition to the significant quantity of make-up water also result in a higher specific fuel demand. |
Required fuel energy per kg of steam to the consumer: |
||
0.724 [kWh/kg] |
0.793 [kWh/kg] (+ 9.5 %) |
0.755 [kWh/kg] (+ 4.3 % ) |
Example calculations of mass and energy balances for various steam systems
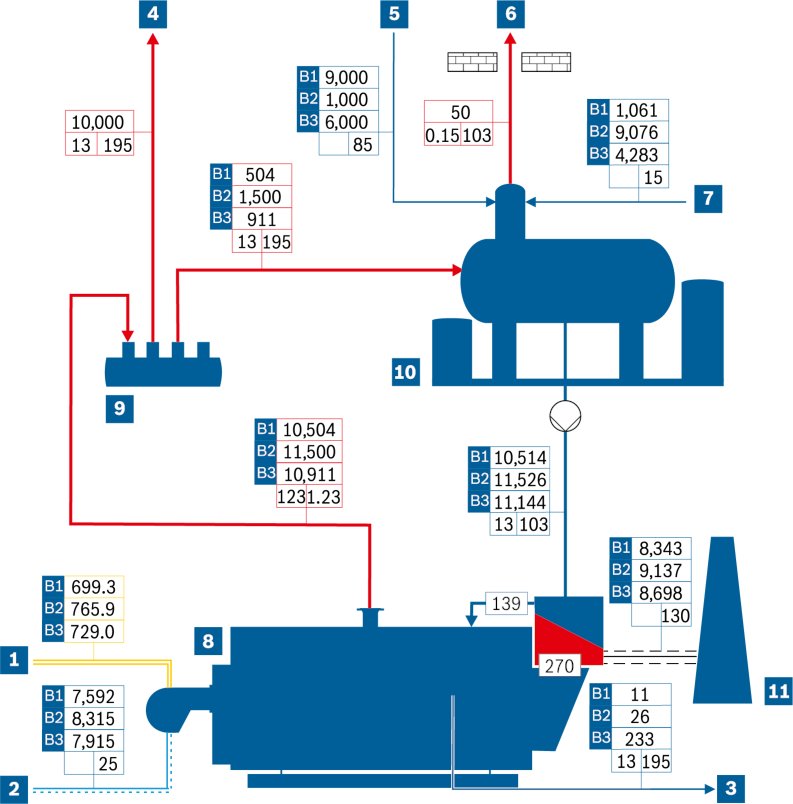
Illustration of mass and energy balance in simplified flow chart (highly-simplified representation)
|
Fuel |
|
Air |
|
Surface blowdown |
|
Saturated steam |
|
Oxygenic condensate |
|
Exhaust vapour |
|
Make-up water |
|
Steam boiler |
|
Steam distributor |
|
Water service module |
|
Chimney |
|
Water |
|
Steam |
|
Fuel |
|
Air |
|
Flue gas |
Mass flow |
|
Pressure |
Temperature |