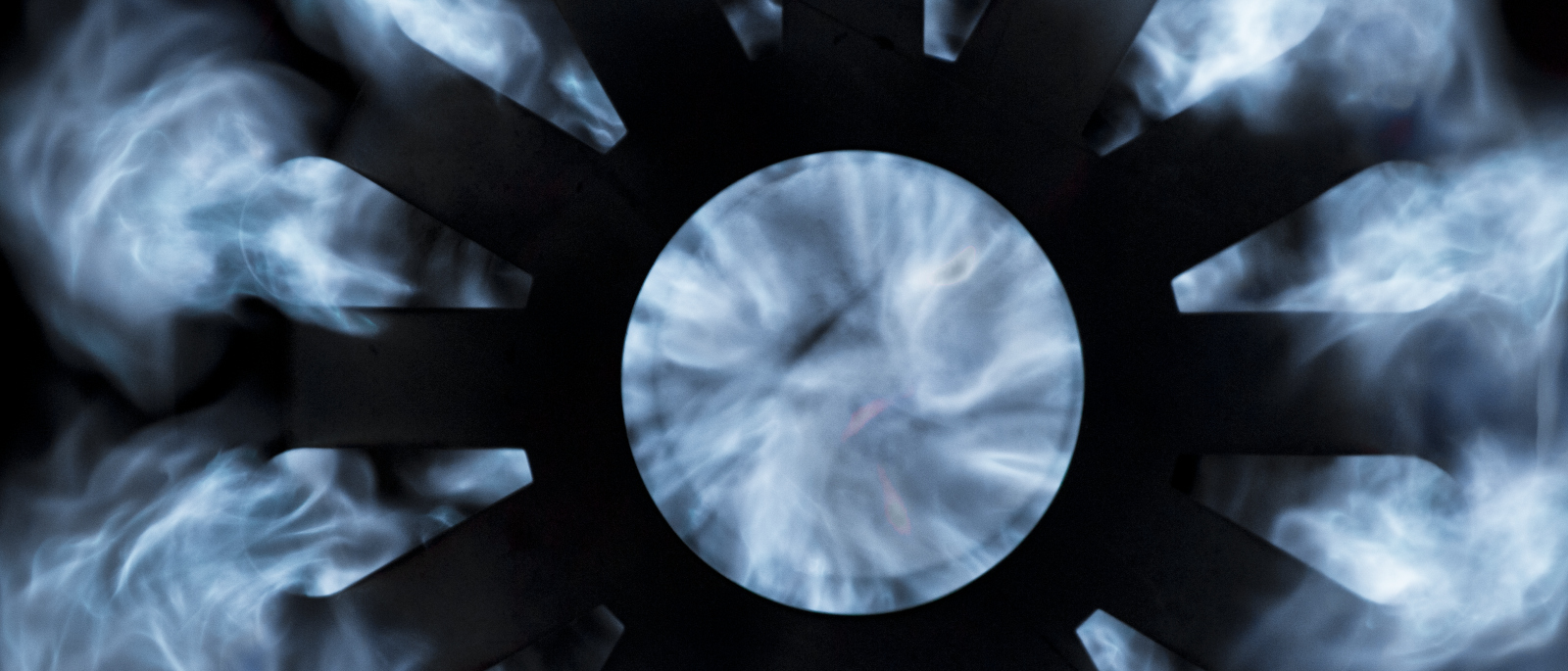
Fuel
The following fuels are used in the majority of steam boiler systems:
- Natural gas
- Fuel oil
These fuels are more or less available everywhere, and to a large extent, standardised and thus have a high quality.
However, other fuels can be used to generate steam:
- Medium oil or heavy oil
- Other gases (e. g. hydrogen, LPG, LNG)
- Biofuels (e. g. lean gases, sewage gases and biogases)
- Contaminated by-products from the chemical industry (e. g. styrene, toluene)
- By-products from other industries (e. g. animal fat, fish oil)
The choice of fuel initially depends on the availability at the planned installation location. Oil is delivered via road tanker, whereas for a gas station, gas transfer from the gas distribution system must be available.
If the requirements for security of supply are high, two fuels can also be used in the same boiler. Gas is then normally used as the main fuel and fuel oil as the substitute fuel.
Economy is another important factor in fuel selection. Exact comparability must be ensured when comparing costs. When using gas as fuel, the comparison price can be obtained directly from the gas bill or requested from the gas provider. The fuel oil supply prices are published on the Internet.
Info on Criteria for selection between fuel oil and natural gas
Apart from the fuel costs, the secondary costs for operation, maintenance and inspection of boiler systems and possibly the occupancy costs for adjacent buildings, must be considered.
Overall, gas-fired boilers tend to be more economical, which is why many existing systems have been converted from oil to gas or dual-fuel burners in the past decade.
In addition to the cost, the impact on the environment during combustion varies, depending on which fuel is used and must be considered. In particular, the permitted emissions at the installation location of the boiler system play a significant role. When used as a fuel, natural gas has a lower pollutant emission in terms of CO2, NOx and SO2 emissions.
Fuel oil
When using mineral oils as a fuel, various additional requirements arising from water pollution and fire prevention regulations, especially in relation to delivery, storage and distribution, must be considered.
Fuel oil EL
The fuel oil type EL, extra light (liquid), is a reliable and readily available source and is normally delivered on a road tanker.
Using Germany as an example, these are the following types of fuel oil EL available:
- Fuel oil EL, standard
- Fuel oil EL, low-sulphur
- Bio fuel oil EL
The most popular type of fuel oil is fuel oil EL low-sulphur, which has a maximum sulphur content of 50mg/kg. Due to the favourable taxation rate, it has in the meantime established a market share of nearly 100%. It is also ideal for condensing technology as it has an even lower soiling tendency than fuel oil EL.
Bio fuel oil EL is low-sulphur fuel oil to which up to 5, 10 or 15% liquid fuel from renewable raw materials is added. Biodiesel is currently used for this as a rule.
The minimum requirements and tests on fuel oil EL are defined in DIN 51603-1.
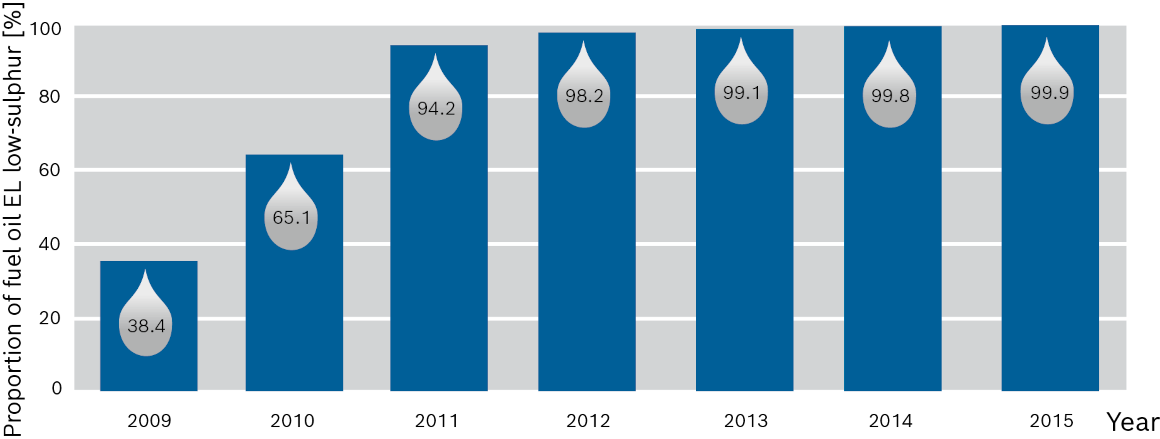
Market share of low-sulphur fuel oil in Germany (IWO – Institute for Heating and Oil Technology)
Heavy fuel oil (HFO)
Heavy fuel oil is used for steam generators more or less exclusively in large industrial systems. It is produced during refinement of crude oil in the bottom part, the so-called sump of the distillation towers, where the components of the crude oil with a high boiling point are removed. It primarily contains large relatively heavy molecules such as long-chain alkanes and alkenes, cycloalkanes and various aromatic hydrocarbons. It also contains various nitrogen and sulphur compounds.
Heavy fuel oil is viscous and must be heated to a temperature of over 60°C in order for it to be able to flow through pipework. The atomisation temperature required for combustion is even between 100 – 160°C. The atomisation viscosity requirements are significantly higher for pressure-jet oil burners than rotary cup oil burners, which is why the fuel oil must be preheated to higher temperatures.
Heavy fuel oil contains up to 3.5 mass percent sulphur, has a tendency to leave heavy deposits in the flue gas path and the flue gas should not be cooled to below the acid dew point of roughly 120 – 150°C. Additionally, special measures are sometimes required (e.g. urea injection) in order to comply with flue gas emissions.
It has many disadvantages compared to using fuel oil EL and natural gas which in general cannot be outweighed by its low price.
Natural gas
Use of natural gas is frequently recommended if a supply of natural gas is available at the planned installation location of the boiler. By connecting to the supply network, there is no need to stock up on fuel and in the deregulated gas market it is easy to switch provider. Far less space is required for the gas transfer station compared to the oil storage tank including ancillary systems. In addition, natural gas from the public network is suitable for unrestricted use with condensing technology.
Info on Condensing heat exchanger
Another thing the fuel gas has in its favour is that the control range for partial load operation is significantly bigger than for oil. While oil burners normally only reach a partial load range of 1:5,
state-of-the-art gas burners can cover twice the partial load range, i.e. a control range of up to 1:10.
The net calorific value of the gas, the gas flow pressure available at the installation location of the boiler and information on the maximum quantities of heat available via the gas connection are required for the design of the fuel supply with gas. This information can be obtained from the local gas system operator.
Criteria for selection between fuel oil and natural gas
The most important factors influencing the selection of fuel are summarised in the following table (Federal Statistical Office):
Criterion |
Fuel oil EL |
Natural gas |
Advantage/disadvantage for natural gas |
Fuel store |
Yes |
No |
+ |
Connection |
No |
Yes |
– |
Available everywhere |
Yes |
No |
– |
Price stability |
No |
Limited yes (Fig. below) |
+ |
Preliminary financing |
Yes (supply) |
No |
+ |
Burner costs |
Neutral |
Increased |
– |
Control range |
up to 1:5 |
up to 1:8 |
+ |
Heating surface soiling |
Low |
None |
+ |
Condensing use |
Good |
Very good |
+ |
Fuel transportation |
Necessary |
Not required |
+ |
Pollutant emission |
Low |
Very low |
+ |
CO2 generation |
~ 266 gCO2/kWh |
~ 200 gCO2/kWh |
+ |
Development of fuel prices for industrial customers Germany (Federal Statistical Office)
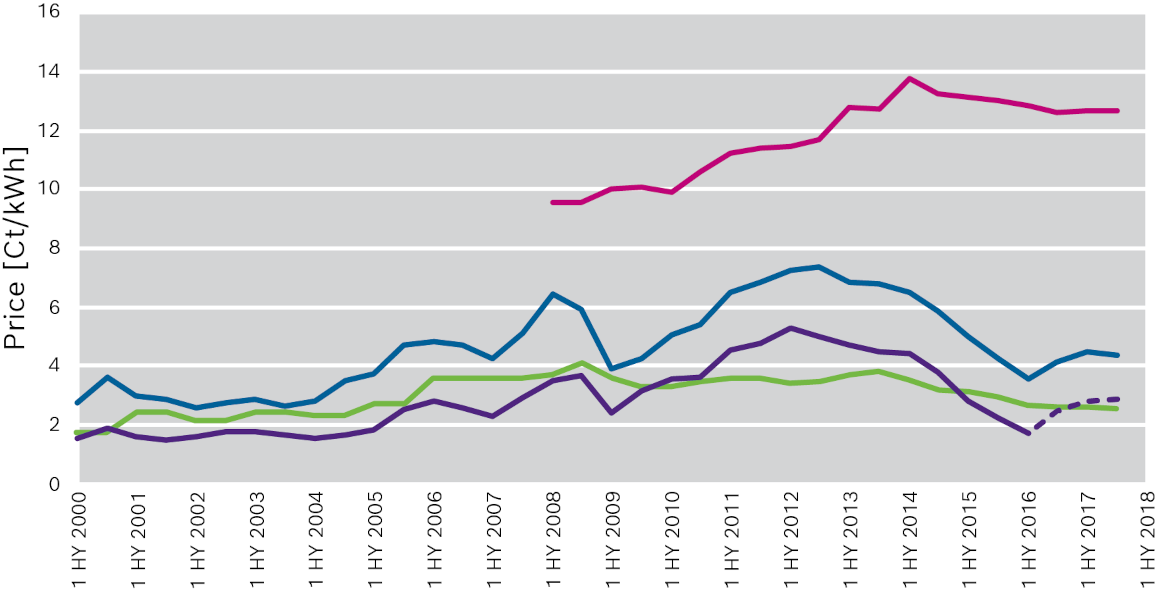
|
Electricity |
|
Heavy fuel oil |
|
|
Light fuel oil |
|
Natural gas |
Notes (Federal Statistical Office):
- Gas, electricity: details for industrial customers, prices include purchase tax and exclude VAT
- Fuel oil: details for wholesale trade, prices include petroleum tax and petroleum stockpiling fee and exclude VAT
- Conversion of prices for fuel oil EL with density 0.84kg/l and net calorific value 11.89kWh/kg
- Conversion of prices for heavy fuel oil with 11kWh/kg
- Heavy fuel oil: specific data only available until December 2016, after this date the data is extrapolated via the price indices
Further fuels
If any other fuels apart from natural gas or fuel oil are used, special attention should be paid in these cases.
The following fuels can also be used:
- Other gases (e. g. hydrogen, LPG, LNG)
- Biofuels (e. g. lean gases, biodiesel, vegetable oils, sewage gases and biogases)
- Contaminated by-products from the chemical industry (e. g. styrene, toluene)
- Secondary products from other industries (e.g. animal fat, fish oil)
The combustion characteristics of these fuels must be taken into account when designing the combustion system, ancillary components, boiler and when devising suitable flue gas heat recovery measures.
The following characteristics in particular must be considered in this context:
- Fuels with high sulphur content (e. g. biogas)
- Fuels containing chlorine (e.g. by-products from the chemical industry)
- Fuels that leave heavy deposits on the heating surfaces (e.g. so-called re-raffinates)
- Fuels with a particularly high net calorific value which therefore subject the flame tube to higher thermal stresses (e.g. hydrogen)