Control de la caldera
El control de la caldera sigue desempeñando un papel decisivo para garantizar un funcionamiento seguro, fiable y económico.
Por lo tanto, deben cumplirse los requisitos de seguridad de las distintas normativas para la instalación y el funcionamiento seguro de los sistemas de calderas. Sin embargo, además de la seguridad y el funcionamiento fiable, hoy en día también son importantes otros requisitos de gestión de la energía, como el registro de datos y la optimización continua del funcionamiento de la caldera. Además, deben estar disponibles todas las opciones para gestionar la producción desde un sistema de automatización central, ya que el funcionamiento optimizado de una planta en términos de rendimiento económico global sólo es posible mediante la comunicación interna entre los consumidores de vapor y los generadores de vapor.
Las tareas básicas del armario de control son:
- Funciones de seguridad
- Funciones de control
- Mensajes de funcionamiento y avería
- Registro y evaluación de datos
- Interfaz de control
- Mantenimiento por tercerose
Desde 2001, Bosch Industriekessel GmbH es el primer fabricante de calderas que utiliza sistemas de control basados en PLC como estándar en las calderas pirotubulares. El concepto se convirtió en un éxito rotundo en el mercado y, entretanto, se ha convertido en equipamiento estándar.
Los sistemas de control están en continuo desarrollo. En combinación con los controladores lógicosprogramables, se consigue un alto grado de transparencia y conectividad de los datos de funcionamientomediante pantallas táctiles con una interfaz gráfica de usuario de manejo intuitivo.
Además del control de la caldera, en un sistema de calderas también deben realizarse una serie de tareas de control adicionales. Estas tareas se tratan junto con la conexión en red de los controles en el capítulo Control del sistema.
Sistema de control
Hoy en día, el hardware del campo de los controladores lógicos programables que se ha probado en aplicaciones industriales se utiliza más o menos en todas partes en los sistemas de control más modernos para llevar a cabo las tareas de control necesarias en la caldera y en la sala de calderas.
Los dispositivos realizan todas las funciones de control de la caldera o del sistema de calderas y pueden comunicarse con otros controles (por ejemplo, sistemas de gestión de quemadores, controles independientes de módulos de la sala de calderas y sistemas de control de procesos de nivel superior) a través de sistemas de bus o redes. Debido a las elevadas exigencias en términos de fiabilidad, la cadena de seguridad se implementa normalmente utilizando la tecnología convencional de contactores y relés.
Todo el software de control se almacena en una tarjeta de memoria micro. Esto evita tener que utilizar baterías de reserva o EPROM para protegerse de los fallos de tensión. Los dispositivos son compactos,modulares y se atornillan a un carril perfilado para formar un conjunto robusto que cumple la normativa CEM. En función de las necesidades, pueden combinarse dispositivos opcionales como entradas y salidas adicionales o un procesador de comunicaciones, como para Profibus DP, para la interconexión con el sistema de automatización central. Existen opciones adicionales, como una red Ethernet industrial para la conexión de varios módulos de control o la preparación para el acceso remoto MEC Remote.
Las complejas y estrictas exigencias para un funcionamiento seguro de la caldera se satisfacen utilizando módulos de funciones de software probados en fábrica y especialmente adaptados a los controles de la caldera y del sistema de calderas en cuestión. El cliente se beneficia de sistemas con una amplia gama de variantes en los que los módulos de software individuales ya se han utilizado y probado muchas veces en la práctica. La programación individual especial sólo se realiza ocasionalmente en casos excepcionales.
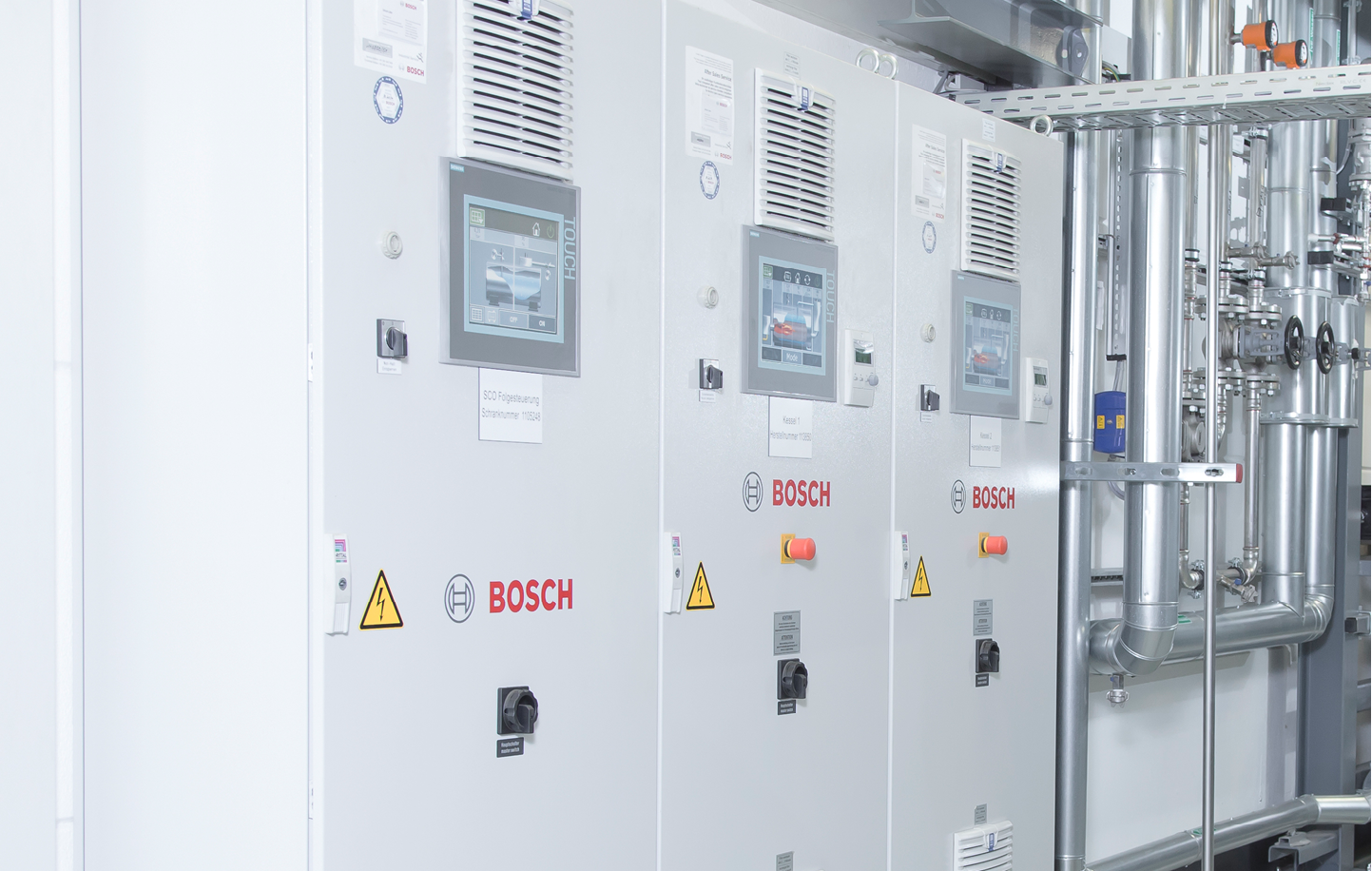
Cuadro eléctrico Bosch