Equipamiento y control
Los requisitos mínimos para el funcionamiento y el equipo de seguridad de las calderas de vapor se establecen en la norma EN 12953-6. Esto incluye las válvulas de cierre primario en las tuberías, el equipo de seguridad para proteger contra el exceso de presión y la falta de agua, el equipo de calefacción y todas las válvulas y dispositivos de medición necesarios para el funcionamiento y el control. Todos estos equipos requieren una homologación de conformidad con la Directiva sobre equipos a presión.
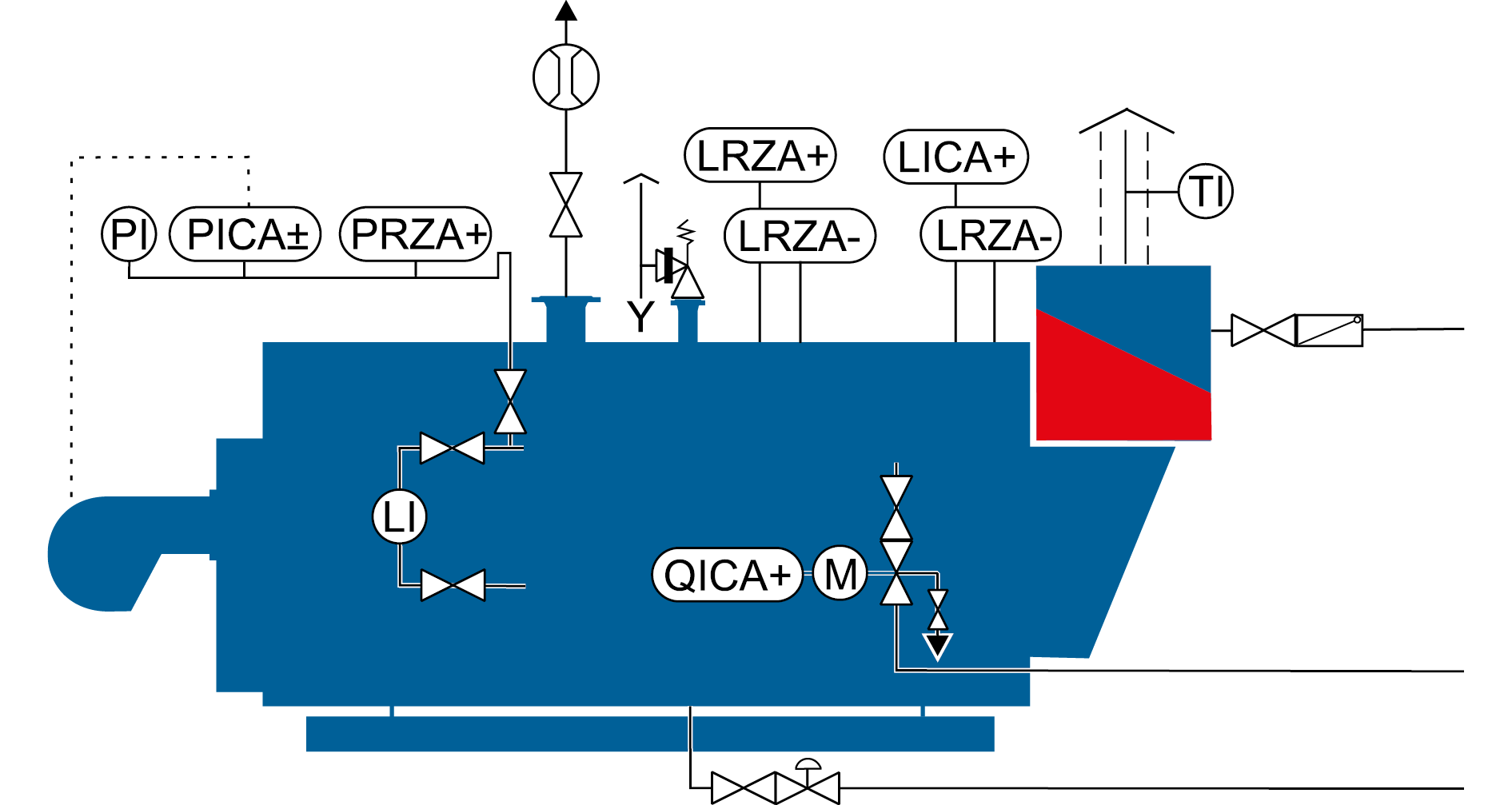
Equipamiento de una caldera de vapor
El equipamiento de una caldera de vapor suele constar de los siguientes componentes:
- Válvula de cierre de extracción de vapor con medición del volumen de vapor
- Válvula de seguridad (protección contra sobrepresión)
- Válvula de corte de agua de alimentación con válvula antirretorno
- Manostato manómetro bar con válvula de cierre, limitador de presión (PRZA+), transmisor de presión (PICA±) y manómetro (PI)
- Dispositivo indicador de nivel directo con válvulas de cierre
- Dispositivo de medición de nivel con tubo protector 1 con limitador de nivel de agua bajo 1 (LRZA-) y transmisor de nivel (LICA+)
- Dispositivo de medición de nivel con tubo protector 2 con limitador de nivel de agua bajo 2 (LRZA-) y limitador de nivel de agua alto (LRZA+)
- Dispositivo de medición de la conductividad (QICA+)
- Válvula de control de purga de superficie con válvula de cierre
- Toma de muestras de agua
- Válvula de purga rápida de fondo con válvula de cierre
- Indicador de temperatura de los gases de combustión (TI)
Pueden ser necesarios componentes adicionales, como dispositivos para medir la cantidad de combustible, vapor, agua de alimentación y la temperatura de los gases de combustión, para optimizar el funcionamiento y para una posible gestión de la energía.
Control de potencia
La producción de vapor de las calderas se controla generalmente a través de la presión existente en la caldera. En este caso, la presión de la caldera se utiliza como variable sustitutiva de la cantidad de vapor. Si los consumidores necesitan más vapor, la presión en la caldera disminuye y el control de potencia aumenta el suministro de calor o la potencia de combustión del quemador. Como norma básica, debe tenerse en cuenta que el sistema de quemador/caldera es un sistema de respuesta lenta. Todas las unidades de control y válvulas mezcladoras que están conectadas a este sistema están ajustadas a estas características. En ningún caso se debe intentar controlar la presión en los consumidores o iniciar medidas en la caldera, ya que esto podría provocar oscilaciones en el control y cargas y averías innecesarias en la caldera. Con un consumo de potencia constante, una regulación correctamente ajustada y un quemador de regulación continua, se establece la potencia de combustión necesaria en el quemador para la tasa actual de extracción de vapor y la presión de la caldera se mantiene constante dentro de unos límites razonables con una desviación de ± 10% del valor nominal especificado.
Informe técnico: control de potencia de las calderas de vapor
La presión existente en la caldera puede leerse directamente en el manómetro (PI). El transmisor de presión (PICA+) mide la presión de la caldera y la convierte en una señal eléctrica estándar (4 – 20mA). Esta señal se procesa en el control de la caldera y se evalúa en función del modo de regulación. El quemador se activa mediante puntos de conmutación y valores de consigna ajustables. En este caso, el control del quemador ajusta la relación combustible-aire correcta.
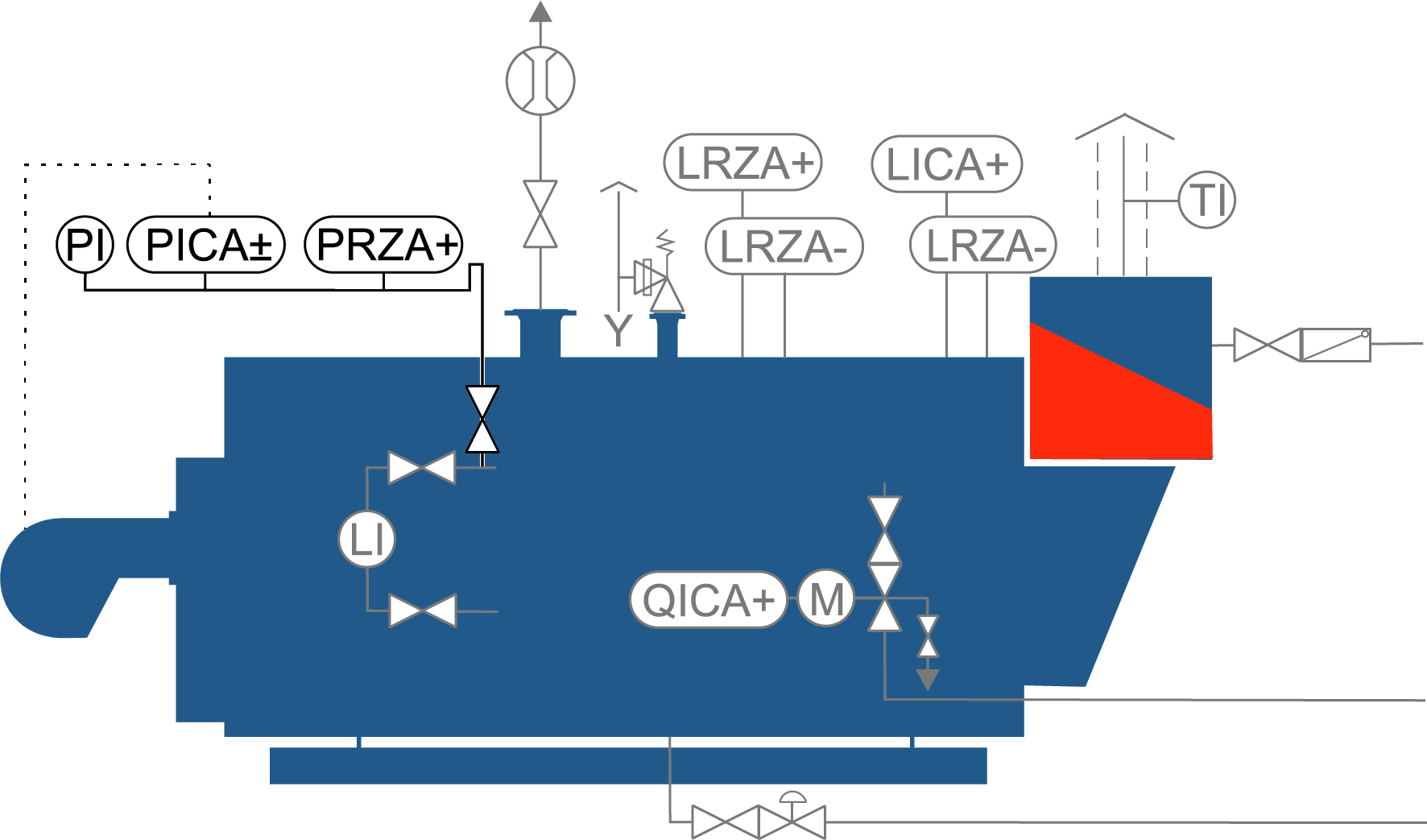
Control de la potencia de una caldera de vapor mediante presión
PI |
Manómetro |
PICA± |
Transmisor de presión |
PRZA+ |
Limitador de presión |
Control de nivel
El control de nivel en la caldera tiene la tarea de mantener un nivel de agua constante en la medida de lo posible. Dependiendo del diseño, el agua fluctúa normalmente entre los límites máximos de 80 – 120mm. El nivel de agua en el rango inferior está limitado visualmente por la marca de agua baja (LW), ya que las superficies de calefacción deben estar siempre bajo el agua para refrigerarse suficientemente. El límite superior del nivel de agua está definido por la marca de agua alta (HW). El espacio de vapor no debe ser demasiado pequeño, ya que de lo contrario podría entrar agua en la tubería de vapor, lo que afectaría negativamente a la calidad del vapor. Para evitar averías y daños en la caldera o en los consumidores posteriores, las posibilidades de ajuste en el regulador de nivel para el nivel medio de agua se han restringido en fábrica. El valor sólo puede ajustarse dentro del rango permitido.
El nivel de agua predominante en la caldera se mide continuamente con el transmisor de nivel (LICA+) y se convierte en una señal eléctrica estándar (4 – 20 mA). Esta señal es procesada por el control de caldera BCO y controla la válvula de control del agua de alimentación o la bomba de alimentación, según el equipo seleccionado.
En la entrada de la caldera o del economizador hay una válvula de cierre y una válvula antirretorno para evitar que el agua vuelva a introducirse en el conducto de alimentación. Se ha instalado un indicador de nivel (LI) en la caldera a la altura del nivel de agua para visualizar directamente el nivel de agua.
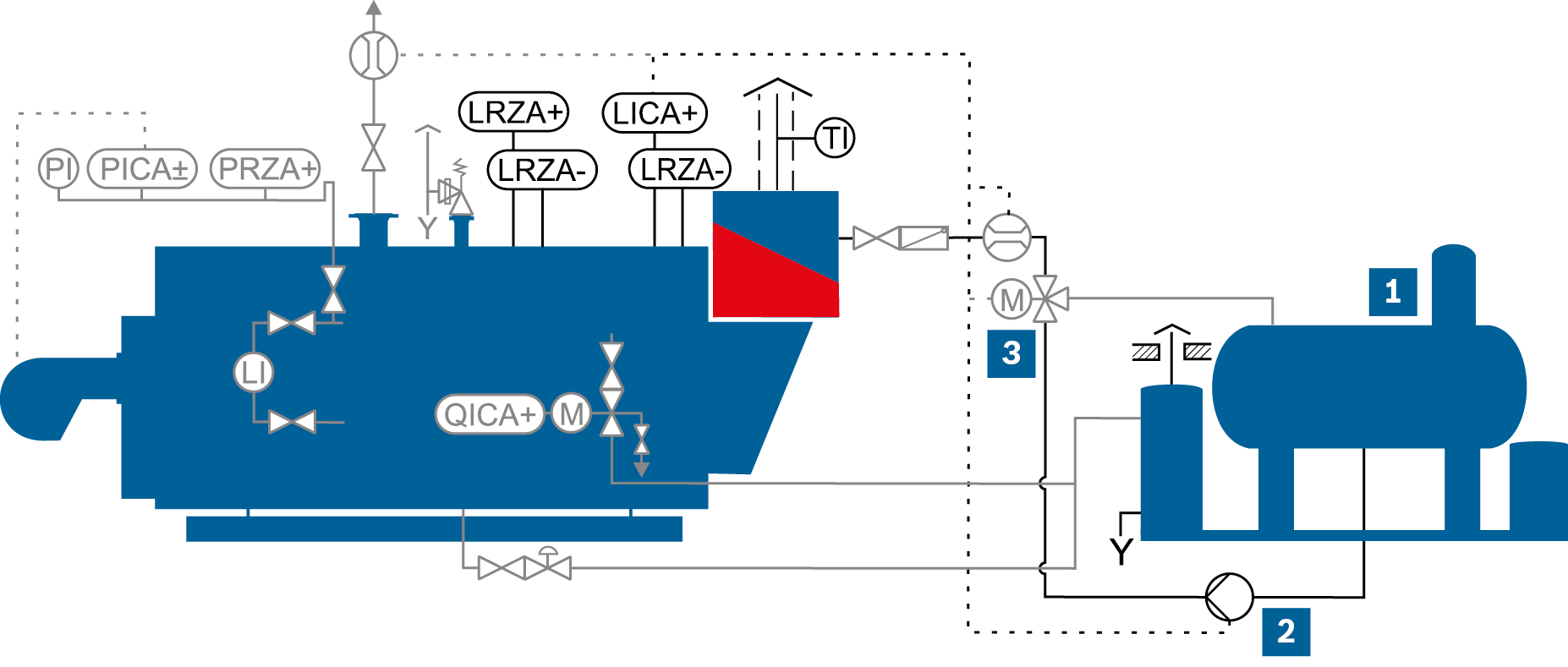
Control de nivel de una caldera de vapor
LICA+ |
Transmisor de nivel |
|
Depósito de agua de alimentación |
|
LRZA+ |
Limitador de nivel de agua alto |
|
Bomba de agua de alimentación |
|
LRZA- |
Limitador de nivel de agua bajo |
|
Válvula de control del agua de alimentación |
|
TI |
Indicador de temperatura de los gases de combustión |
Además del control de nivel, el nivel de agua también se limita mediante la cadena de seguridad.
Recuperación de calor con ECO |
Requisitos de las características de control |
Proceso caracterizado por cambios rápidos de carga |
Costos de inversión |
|
Continuo con válvula de control |
+++++ |
+++++ |
++ |
Moderado |
Barra colectora con válvula de control1) |
+++++ |
+++++ |
++ |
Bajo |
Continuo con IM2) |
++++ |
+++ |
++ |
Bajo |
Control de 3 componentes con válvula de control |
+++++ |
+++++ |
+++++ |
Muy alto |
Control de 3 componentes conIM |
++++ |
+++ |
+++++ |
Alta |
ON/OFF |
No |
+ |
Muy bajo |
Ventajas y posibles usos de los distintos tipos de control de nivel
1) Sólo puede utilizarse con sistemas de varias calderas
2) IM = módulo inversor
Control modulante con válvula de control
El control de nivel continuo con válvula de control sigue siendo la variante más popular, ya que ofrece las ventajas de un control rápido, fiable y sencillo.
Productos: Módulo de regulación del agua de alimentación RM
Conmutación de barras con válvula de control
Cuando se utiliza la conmutación de barras, una bomba de alimentación alimenta varias calderas de vapor. En este caso, el nivel de agua de cada caldera se controla de forma independiente mediante una válvula de control de entrada.
Control modulante con módulo inversor
La regulación del nivel mediante el control de velocidad en la bomba de alimentación es la variante más económica para potencias de calderas ≤ 10 t/h en términos de costes de inversión y costes de operación.
Además, tiene especial sentido utilizar este tipo de control de nivel si la caldera funciona a diferentes presiones de funcionamiento (por ejemplo, una caída de presión en el fin de semana), ya que entonces se pueden aprovechar al máximo las ventajas del control de velocidad con adaptación a la curva de la bomba.
Si se equipa la caldera con un economizador para la recuperación de calor, debe garantizarse que el rango de carga parcial del quemador también pueda cubrirse con el rango de regulación de frecuencia más pequeño de la bomba de alimentación, ya que, de lo contrario, no hay caudal a través del economizador en funcionamiento con carga baja, lo que significa que no puede producirse la recuperación de calor.
Control de 3 componentes
Cuando la carga aumenta rápidamente, se produce un problema ya que el nivel de agua parece aumentar inicialmente debido a la formación de espuma en el agua de la caldera y, aunque es necesario aumentar la cantidad de agua de alimentación, esto no ocurre.
Al comparar continuamente las mediciones de corriente para las cantidades de vapor y agua de alimentación, el control de 3 componentes puede responder mucho más eficazmente a los cambios de estado.
Control On/Off
La activación/desactivación de las bombas sólo se utiliza en algunos casos excepcionales y con potencias de vapor bajas, de hasta ~ 1 t/h.
Dado que, en comparación con las demás variantes de control, el beneficio en términos de costes de inversión es relativamente bajo y que se recupera mucho menos calor en el economizador porque las bombas se desconectan con frecuencia, un control continuo suele amortizarse en menos de dos meses.
Calidad de agua
En función de los distintos métodos físicos y químicos de tratamiento del agua, de la dosificación química para ligar la dureza residual y el oxígeno residual y de la alcalinización necesaria (aumento del valor pH en el depósito de agua de alimentación), el agua de alimentación contiene sales disueltas y otros ingredientes.
Info sobre Tratamiento de agua
Debido al continuo proceso de evaporación cuando la caldera está en funcionamiento, aumentan los ingredientes residuales del agua de alimentación en el agua de la caldera. La acumulación de impurezas en el agua de la caldera es especialmente medible debido al aumento de la conductividad del agua de la caldera.
Para evitar las consecuencias negativas de un contenido excesivo de sales en el agua de la caldera que se describen a continuación, no deben superarse los límites especificados.
- Formación de espuma en el agua de la caldera
- Arrastre de agua en la tubería de vapor
- Fluctuaciones del nivel de agua
- Depósitos en la caldera
- Corrosión en la caldera y las tuberías
Informe técnico: tratamiento moderno y análisis del agua
Por lo tanto, se elimina una cierta cantidad de agua de la caldera como resultado de la continua purga de superficie y la purga de fondo.
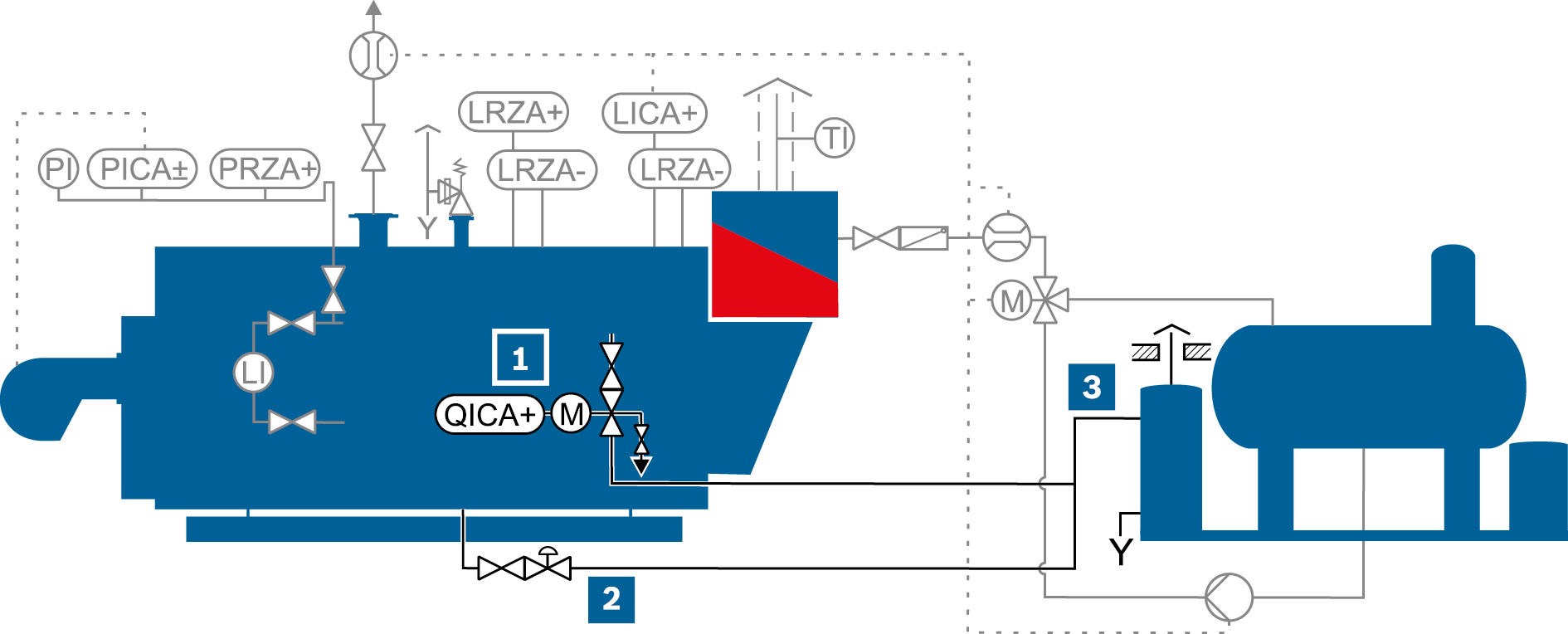
Control de la calidad del agua de caldera mediante descarga al depósito de expansión de purga
QICA+ |
Transmisor de conductividad |
|
Válvula de purga de superficie |
|
|
Válvula de purga de fondo |
|||
|
Depósito de expansión de la purga |
Control de la conductividad
La conductividad del agua de la caldera se mide con el transmisor de conductividad (QICA+) y se convierte en una señal eléctrica estándar (4 – 20 mA). Esta señal se procesa en el control de caldera BCO, la conductividad medida se muestra en el armario de control y se genera la señal de accionamiento para abrir la válvula de purga de superficie motorizada. Para poder realizar una inspección visual, a menudo se instala una mirilla con válvula antirretorno en la tubería aguas abajo de la válvula de purga de superficie.
Dado que la calidad del agua de la caldera es un factor importante que influye en el funcionamiento correcto y sin problemas, debe comprobarse periódicamente y documentarse en el registro de la caldera.
Se pueden adoptar medidas de recuperación de calor para aprovechar el contenido energético del agua de purga de superficie en ebullición.
Info sobre Purga de superficie y purga de fondo
La conductividad medida en la caldera a la temperatura de funcionamiento es ligeramente superior debido a la disociación electrolítica. El sensor de conductividad realiza internamente una conversión utilizando la temperatura de referencia de 25°C. Esta conductividad preajustada se muestra en el control de la caldera.
Además de la conductividad eléctrica, el contenido de ácido silícico (SiO2) y el valor de capacidad ácida 8.2 (valor p) son factores importantes que influyen en la calidad del agua de la caldera. Si se alcanza el límite admisible de una de estas variables debido a la densificación en el agua de la caldera, esta variable es definitiva para la purga superficial. Sin embargo, como sólo se mide la conductividad en el agua de la caldera, el valor de referencia de la conductividad en el agua de la caldera debe reducirse hasta que puedan respetarse todas las variables límite.
Control de purga de fondo
El control de purga de fondo elimina las materias en suspensión del agua de la caldera que se depositan en el fondo de la misma. Para ello, la válvula de descarga de fondo se abre durante unos segundos a intervalos regulares. La válvula se abre bruscamente, lo que produce una presión negativa local con un efecto de aspiración que elimina de la caldera los depósitos que se han acumulado en el fondo de la caldera (por ejemplo, acumulaciones de sales, agente dosificador descompuesto).
Los tiempos de apertura de la válvula durante este proceso deben ser muy cortos y estar dentro del rango de unos pocos segundos. Si los tiempos de apertura de la válvula de purga de fondo son más largos, esto sólo aumenta la pérdida de agua y energía de la caldera sin hacer que la purga de fondo sea más eficaz. La purga de fondo puede realizarse manual o automáticamente si la caldera no está atendida continuamente durante el funcionamiento.
Antes de la válvula de purga de fondo se instala una válvula de cierre manual. Para favorecer el efecto de aspiración y permitir la evacuación del agua de la caldera que se ha evaporado de nuevo, las tuberías que conducen al depósito de expansión de la purga directamente aguas abajo de la válvula deben ser 2 diámetros nominales mayores. Para evitar los golpes de ariete, las tuberías que conducen al depósito de expansión de purga deben instalarse, siempre que sea posible, sin cambios de altura ni bolsas de agua.
La mayoría de las calderas también se vacían a través de la válvula de purga inferior.
Seguridad
La seguridad del sistema se garantiza principalmente mediante un funcionamiento correcto, una funcionalidad perfecta y el mantenimiento de los equipos y las unidades de control de las calderas de vapor.
Para garantizar la seguridad en todo momento, también cuando fallan las unidades de control normales, se prescriben dispositivos limitadores para todas las calderas de vapor. Junto con los botones de parada de emergencia del armario de control y las puertas de escape, están conectados en serie en la cadena de seguridad del armario de control de la caldera, de modo que cuando se dispara uno de estoselementos, se desactiva el funcionamiento de la caldera.
Si se dispara uno de los dispositivos limitadores, se desconecta y bloquea el sistema de combustión y, por tanto, la calefacción de la caldera. En las calderas de calor residual, esto se hace cambiando las compuertas de gases de combustión a bypass o desconectando la unidad generadora de calor. Este bloqueo sólo puede volver a activarse manualmente en la caldera. De este modo se garantiza que, tras condiciones de funcionamiento excepcionales, el encargado de la caldera haya identificado y eliminado la causa de la avería antes de volver a poner la caldera en funcionamiento.
Limitador de presión de seguridad
El limitador de presión de seguridad (PRZA+) se activa al 95 % de la presión de funcionamiento máxima admisible y desconecta la calefacción de la caldera.
Válvula de seguridad
La válvula de seguridad debe impedir de forma fiable que se supere la presión máxima admisible en la caldera si falla el limitador de presión de seguridad.
En las calderas pirotubulares, esto se consigue mediante válvulas de seguridad de muelle de acción directa de carrera completa con bonete de muelle abierto.
Una vez que la válvula de seguridad ha actuado, la presión en la caldera debe descender aproximadamente un 10 % por debajo de la presión máxima admisible antes de que la válvula de seguridad se cierre automáticamente debido a la tensión del muelle. En la medida de lo posible, las tuberías posteriores deben conducirse directamente a la atmósfera.
Indicador de nivel de agua baja
Las superficies de calentamiento de la caldera deben estar rodeadas de agua en todo momento para garantizar una refrigeración suficiente. Si el nivel de agua de la caldera desciende hasta el punto de que las superficies de calefacción dejan de estar en contacto con el agua, existe un grave peligro de sobrecalentamiento y posible destrucción de la caldera.
Para estar seguros de evitar que las superficies de calefacción salgan a flote, se instalan en la caldera dos indicadores de nivel de agua bajo de tipo comprobado que funcionan independientemente el uno del otro. En los generadores de vapor, el electrodo del indicador de nivel se instala en un tubo protector para evitar un mal funcionamiento peligroso debido a la formación de espuma en el agua de la caldera.
Indicador de nivel de agua alta
En los sistemas de calderas que funcionen durante un período de 72 horas sin asistencia, se requiere un indicador adicional de nivel de agua alto para que cuando se supere el nivel de agua más alto permitido en la caldera no pueda introducirse agua en las tuberías de vapor aguas abajo.
Limitación de la conductividad
La conductividad máxima admisible también está limitada en los sistemas de calderas durante un periodo de 72 horas de funcionamiento sin asistencia para evitar la formación incontrolada de espuma o la acumulación de depósitos en la caldera. Cuando se supera el límite, en este caso también se desconecta el sistema de combustión.
Otros equipos de seguridad
El sistema de combustión puede desconectarse por otros fallos además de los dispositivos limitadores montados directamente en la caldera de vapor. Las modificaciones precisas para el combustible correspondiente y los distintos equipos se describen en la norma EN 12953 parte 9.
Parada de emergencia
Los botones de parada de emergencia están instalados en todas las vías de evacuación y en el armario de control de la caldera. Cuando se pulsa un botón de parada de emergencia, se activa la cadena de seguridad de la caldera. Se recomienda instalar un botón de parada de emergencia adicional fuera de la sala de calderas.
Monitorización del sistema de combustión – monitorización de la llama
Si no se detecta una llama en la cámara de combustión cuando la alimentación de combustible está en funcionamiento, se produce una desconexión por avería de la caldera al cabo de unos segundos. De este modo se evita que el combustible no quemado forme una mezcla inflamable en el sistema de gases de combustión que podría provocar un encendido difícil durante un arranque posterior del quemador.
Monitorización del sistema de combustión – alimentación de combustible
La estanqueidad de la válvula de cierre de gas y la presión mínima y máxima de la alimentación de combustible también se controlan para garantizar que no pueda formarse una mezcla inflamable en la caldera o en el recorrido de los gases de combustión.
Fig. Ejemplo de representación esquemática de la combustión de gas (alimentación a alta presión)
Monitorización del sistema de combustión – dispositivo de seguridad contra deficiencias de aire
El funcionamiento y la función del ventilador de aire de combustión se controlan mediante lo que sedenomina un dispositivo de seguridad de deficiencia de aire. Para ello, se instala un indicador de presión de aire mínima (PZA) entre el ventilador y la cabeza de la llama.
Suministro de vapor
El conector de alimentación de vapor con válvula de cierre se encuentra en la corona de la caldera. Desde aquí se alimenta el vapor saturado a la red de vapor aguas abajo. Para limitar la emisión de ruido, el conector de alimentación de vapor debe dimensionarse de modo que la velocidad de flujo no pueda superar ≥ 40m/s. También debe tenerse en cuenta que el diámetro del conector debe dimensionarse con referencia a la presión de funcionamiento mínima prevista, ya que el mayor volumen específico de vapor existe a esta presión.
Debajo del conector, en el interior de la caldera, hay una placa deflectora para garantizar que las pequeñas gotas arrastradas por el flujo permanezcan en la caldera y que el vapor que sale de la caldera esté lo más seco posible. El contenido de humedad residual puede llegar a ser del 3%.
Para mejorar la calidad del vapor, también se puede montar aquí un desempañador de malla metálica. Esto puede reducir el contenido de humedad residual a aproximadamente un 0.1%.
Equipo de medición opcional
Los dispositivos de medición adicionales, por ejemplo para medir el caudal y la temperatura, proporcionan información más detallada sobre el funcionamiento de la caldera. Por un lado, pueden integrarse en el control de la caldera para satisfacer exigencias más estrictas en relación con la calidad del control. Por otro lado, son un medio importante para evaluar la eficacia del funcionamiento de la caldera. Mediante la adquisición, el registro y la evaluación de estos datos, también se puede optimizar el funcionamiento de la caldera tras la puesta en servicio (por ejemplo, en caso de cambios en el funcionamiento). Además, de este modo también pueden satisfacerse los requisitos derivados de cualquier sistema interno de gestión de la energía existente. A continuación se describen los métodos de medición más habituales.
Medición del volumen de vapor
Con la medición del volumen de vapor, se mide el caudal de vapor suministrado a la red de vapor. En combinación con una medición de la presión o la temperatura con vapor saturado o una medición de la presión y la temperatura con vapor sobrecalentado, el volumen de vapor puede convertirse en un caudal de vapor y en la producción de calor útil suministrada por la caldera.
Medición del caudal de agua de alimentación
Durante la medición del caudal de agua de alimentación, se mide el agua de alimentación suministrada a la caldera.
Medición del flujo de combustible
La medición del caudal de combustible es necesaria para cada sistema de calderas individual a fin de poder ajustar la potencia de combustión máxima admisible durante la puesta en servicio.
Con combustibles líquidos, la medición se realiza siempre con asignación directa a una caldera. El caudal de combustible se mide en [l/min] o [l/h].
Con combustibles gaseosos, se recomienda urgentemente una medición asignada directamente a la caldera. Por razones de costes, en ocasiones se omite y se utiliza la medición del proveedor de energía en la estación de transferencia de gas. La medición del caudal de gas en [mB³/h] debe convertirse posteriormente [mn³/h] junto con una medición de la presión y la temperatura a efectos de evaluación.
Junto con la información sobre el valor calorífico neto [kWh/kg] o [kWh/l] para combustibles líquidos y [kWh/mn³n] para combustibles gaseosos, se puede realizar una conversión a la cantidad de energía suministrada a la caldera y, por tanto, utilizarse como base de partida para un cálculo de eficiencia o para determinar el grado de utilización anual.
Medición de la temperatura de los gases de combustión
La medición de la temperatura de los gases de combustión es un indicador importante del modo de funcionamiento actual de la caldera. Muchas opciones de optimización y el funcionamiento antieconómico de la caldera o el ensuciamiento de las superficies de calefacción pueden identificarse inmediatamente simplemente utilizando esta sencilla medición de bajo coste y registrando y evaluando continuamente la temperatura de los gases de combustión.