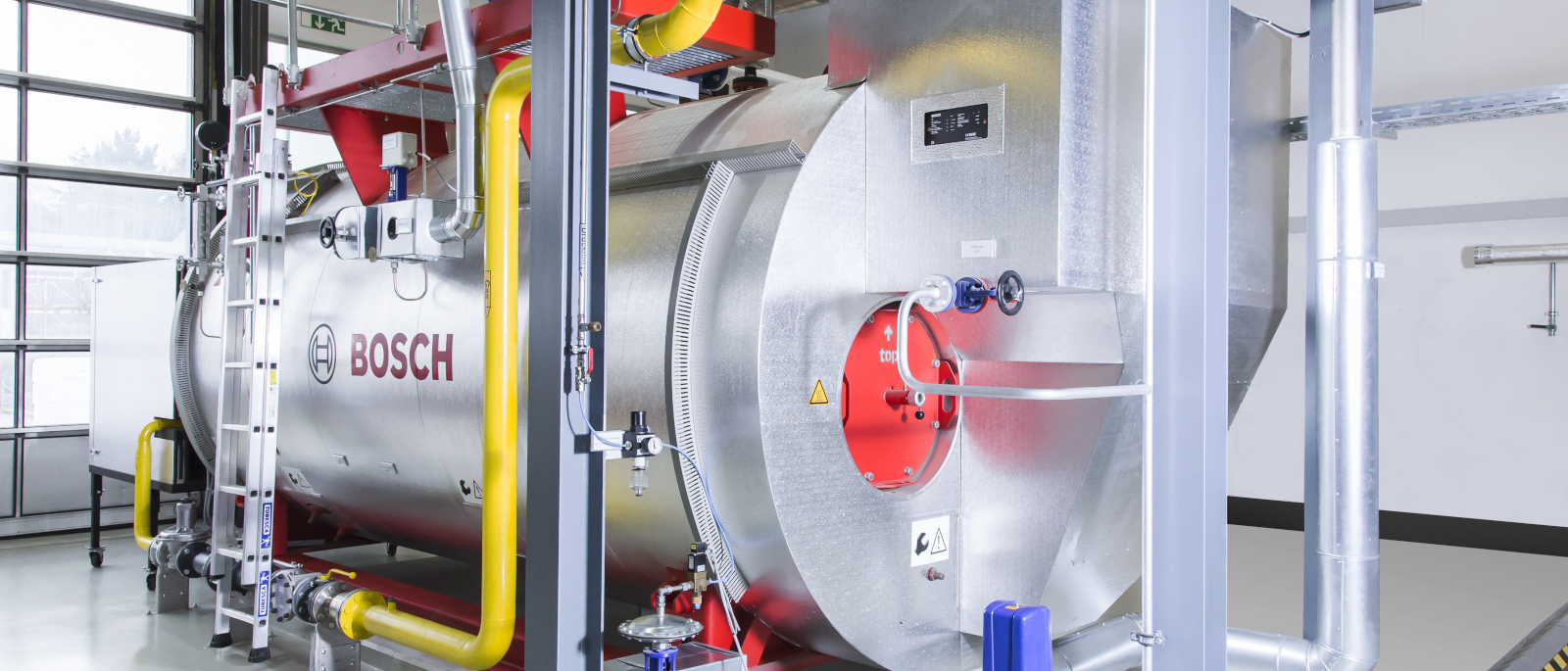
Aumento de la eficiencia de la caldera y del sistema
Aislamiento
Las pérdidas por conductividad y radiación se producen debido a la diferencia de temperatura entre el medio en calderas de vapor, líneas y válvulas y el entorno. La magnitud de las pérdidas de calor depende esencialmente de la superficie, el medio, la temperatura ambiente y el diseño del aislamiento.
Como estas pérdidas no dependen de la potencia, se producen continuamente, también en las fases de inactividad, por lo que también están presentes los 365 días del año en sistemas o partes de sistemas que no se han puesto fuera de servicio. Afectan negativamente al grado de utilización anual del sistema de calderas, especialmente si el sistema funciona frecuentemente en carga parcial.
Info sobre Grado de utilización anual
Además de una investigación con una cámara termográfica, los "puntos calientes", o zonas en las que se producen las mayores pérdidas de calor, pueden detectarse y eliminarse palpando las zonas calientes, inspeccionando visualmente el aislamiento o utilizando un termómetro de superficie o de radiación.
Sin embargo, la temperatura de la superficie sólo refleja hasta cierto punto el grado de pérdida de calor. Especialmente cuando se comparan diferentes materiales superficiales, una temperatura superficial baja es a veces un indicio de mayores pérdidas de calor.
La razón radica en el coeficiente de radiación de la superficie aislante. Si el coeficiente es mayor, las pérdidas de calor aumentan, pero al mismo tiempo disminuye la temperatura de la superficie. Por lo tanto, es ventajoso utilizar un material con un coeficiente de emisión ε bajo.
Ejemplo: |
|
Depósito de agua de alimentación |
L = 3,600 mm, Ø = 1,700 mm |
Aislamiento |
T = 100 mm |
Temperatura del medio |
103 °C |
Material de superficie1) |
Coeficiente de emisión ε |
Pérdidas de calor por |
Temperatura de la superficie |
Aluminio laminado liso |
0.05 |
627.5 W |
30.0 °C |
Aluminio oxidado |
0.13 |
635.5 W |
29.0 °C |
Chapa galvanizada desnuda |
0.26 |
645.5 W |
27.6 °C |
Chapa galvanizada, polvorienta |
0.44 |
655.5 W |
26.3 °C |
Acero inoxidable austenítico |
0.15 |
637.2 W |
28.7 °C |
Chapa de aluminio-cinc ligeramente oxidada |
0.18 |
639.7 W |
28.4 °C |
Superficie no metálica |
0.94 |
671.2 W |
24.2 °C |
1) Según VDI 2055 Hoja 1 Apéndice A8
Las mayores pérdidas de calor en los sistemas existentes se producen normalmente como consecuencia de válvulas sin aislar, zonas que no se han vuelto a aislar tras una inspección o reparación o puentes térmicos que se forman al desplazar la capa protectora de aislamiento.
La mayoría de las pérdidas de calor por conducción y radiación en los sistemas existentes pueden evitarse eliminando estos "puntos calientes" sin tener que volver a aislar completamente el sistema. El aislamiento de las zonas no aisladas de todo el sistema (por ejemplo, caldera, tuberías de vapor y condensado, válvulas, depósitos) es una de las medidas de ahorro más eficaces en los sistemas existentes.
La pérdida de calor en la propia caldera también puede determinarse fácilmente en estado de reposo. La caída de presión puede determinarse una vez que la caldera se ha apagado (por ejemplo, el fin de semana) con las válvulas de vapor, purga de superficie y purga de fondo cerradas. Partiendo de una presión de vapor en la caldera de 10 bar, la caída de presión no debe ser superior a 0.2 bar/h. Hay que tener en cuenta que no sólo hay que considerar las pérdidas por radiación y conducción, sino también las pérdidas por ventilación debidas a la resistencia de la chimenea (si procede). El resultado también puede verse influido por válvulas que no cierren herméticamente.
Sin embargo, la pérdida de calor medida indirectamente a través de la caída de presión está presente independientemente de la causa, y debe evitarse.
La eficacia del aislamiento puede mejorarse teniendo en cuenta los siguientes puntos.
Espesor y superficie del aislamiento
La temperatura superficial y las pérdidas de calor pueden reducirse aumentando el grosor del aislamiento. En este caso, sin embargo, el objetivo es elegir una medida de optimización que sea sensata y económica, ya que las pérdidas superficiales no pueden reducirse en absoluto a la mitad simplemente duplicando el grosor del aislamiento.
Además del grosor del aislamiento, el tamaño de la superficie también desempeña un papel decisivo. Los tipos de caldera compactos, por ejemplo con diseño asimétrico, así como un economizador integrado y la consiguiente menor superficie de aislamiento son ventajosos a este respecto.
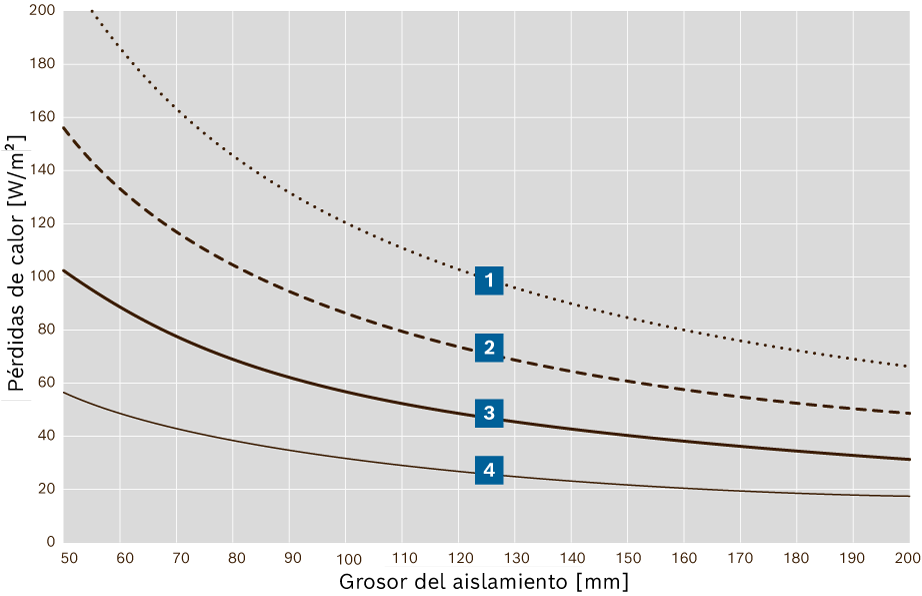
Pérdidas de calor a través de la zona aislada del recipiente o de la superficie de la caldera
|
Temperatura media: 250 °C (. . . . . .) |
|
Temperatura media: 150 °C (_______) |
|
|
Temperatura media: 200 °C (- - - -) |
|
Temperatura media: 100 °C (_______) |
La figura anterior muestra que con un grosor de aislamiento de 100 mm y una temperatura media de 150°C la pérdida de calor es de aproximadamente 57W/m².
Este valor disminuye en un 30% hasta unos 40W/m² cuando el grosor del aislamiento aumenta hasta 150mm. La pérdida de calor puede reducirse en un 44% hasta 32W/m² aumentando el grosor del aislamiento de 100mm a 200mm.
Esto se aplica únicamente a las zonas aisladas sin puentes térmicos en cada caso. Dado que las pérdidas a través de estos puentes pueden superar rápidamente las pérdidas en la zona cilíndrica bien aislada, deben tenerse siempre en cuenta y, siempre que sea posible, minimizarse.
Aislamiento de tuberías
Para ahorrar energía y cumplir los requisitos de salud y seguridad en el trabajo, actualmente es obligatorio aislar de forma continua las tuberías que transportan medios calientes en todas las partes del sistema. Sin embargo, no sólo la normativa, sino también, y sobre todo, los aspectos económicos son decisivos a la hora de decidir qué grosor de aislamiento utilizar.
Tanto la pérdida de calor absoluta por metro lineal de tubería sin aislar (ordenada izquierda) como el factor de ahorro de una sección de tubería aislada (ordenada derecha) pueden determinarse con referencia a la temperatura del medio, el diámetro de la tubería y el grosor del aislamiento a partir del siguiente diagrama.
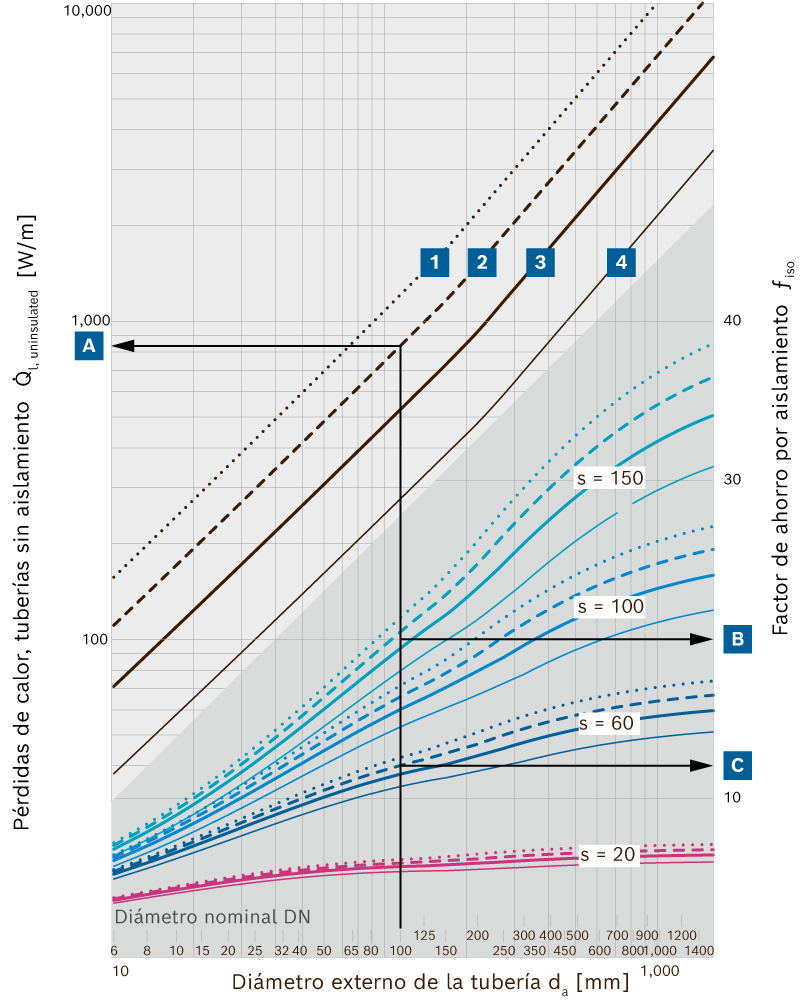
Factor de ahorro debido al aislamiento y las pérdidas de calor en las tuberías
|
Temperatura media: 250 °C (. . . . . .) |
|
Temperatura media: 200 °C (- - - -) |
|
Temperatura media: 150 °C (_______) |
|
Temperatura media: 100 °C (_______) |
|
Grosor del aislamiento s = 150 mm |
|
Grosor del aislamiento s = 100 mm |
|
Grosor del aislamiento s = 60 mm |
|
Grosor del aislamiento s = 20 mm |
|
Pérdida de calor sin aislamiento |
|
Ahorro gracias al aislamiento |
|
Ahorro gracias al aislamiento |
Los cálculos del diagrama anterior se basan en la norma VDI 2055 hoja 1: tubería de acero pintado sin aislar, aislamiento de lana mineral, cubierta aislante de chapa de aluminio, tubería horizontal, temperatura ambiente 20°C.
Aumentar el grosor del aislamiento de una tubería de 100m de 60mm a 150mm ahorra unos €920 anuales (sobre la base de 8,000 horas de funcionamiento y unos costes energéticos de 4.5ct/kWh).
En este caso, cada metro de tubería sin aislar cuesta más de €300 al año.
Ejemplo |
Grosor del aislamiento |
Pérdidas de calor en tuberías |
Pérdida total de calor1) |
Ahorro absoluto2) |
Porcentaje de ahorro2) |
Costes ahorrados2) |
A |
sin aislamiento |
837.0 |
669,600 |
--- |
--- |
|
B |
s = 60 |
66.4 |
53,120 |
--- |
--- |
|
C |
s = 150 |
40.8 |
32,640 |
20,480 |
38.6 |
921.60 |
Ejemplo de ahorro potencial como resultado de aumentar el espesor del aislamiento, basado en una tubería de vapor
1) Basado en 100m de longitud de tubería y 8,000 horas de funcionamiento/año
2) Con referencia al espesor del aislamiento s = 60mm
Minimizar los puentes térmicos
Los puentes térmicos se producen invariablemente cuando las conexiones metálicas con una conductividad térmica muy alta rompen el aislamiento. Este es el caso, por ejemplo, de los conectores, los soportes de calderas o los soportes de plataformas.
En la zona de la cubierta aislante protectora debe garantizarse especialmente que las penetraciones necesarias por motivos funcionales no entren en contacto directo con la cubierta aislante, ya que de lo contrario se crearían puentes térmicos en estos puntos a través de los cuales se perdería energía. Una forma fiable de evitarlo es simplemente envolviendo los conectores en tejido aislante. Los elementos cuya finalidad sea mejorar la estabilidad y rigidez estructural, deben estar dentro del aislamiento para que no puedan conducir el calor hacia el exterior, a la cubierta aislante protectora.
Del mismo modo, no deben utilizarse espaciadores con carcasas cilíndricas, ya que también actúan como puentes térmicos. De este modo se evita la conducción de calor desde el tambor caliente de la caldera a la camisa de aislamiento de protección y el rendimiento de aislamiento térmico de la estera aislante es completamente eficaz.
Aperturas de inspección aisladas
Las calderas de vapor están sujetas a inspecciones internas periódicas por parte de los organismos de control pertinentes. Se requieren aberturas en la cubierta aislante para los orificios de inspección, como los orificios de mano o los orificios de cabeza, o las bocas de inspección. Estas aberturas están aisladas y selladas con tapas aislantes desmontables.
Las aberturas de limpieza e inspección de las cámaras de recogida de gases de combustión y las carcasas de los economizadores se sellan utilizando la misma tecnología de aislamiento para que no se pierda el exceso de calor radiante a través de las aberturas de inspección. Los orificios de inspección se señalan con etiquetas.
Especialmente después de las inspecciones o si se han retirado las cubiertas aislantes por cualquier otro motivo, debe garantizarse que el aislamiento se vuelva a instalar en las aberturas de inspección.
Si no se vuelve a sellar una abertura de inspección con una superficie aproximada de 0.5m², esto significa que a una presión de funcionamiento de 10 bares y una temperatura de 185°C pérdida de energía por día es de aproximadamente 15kWh.
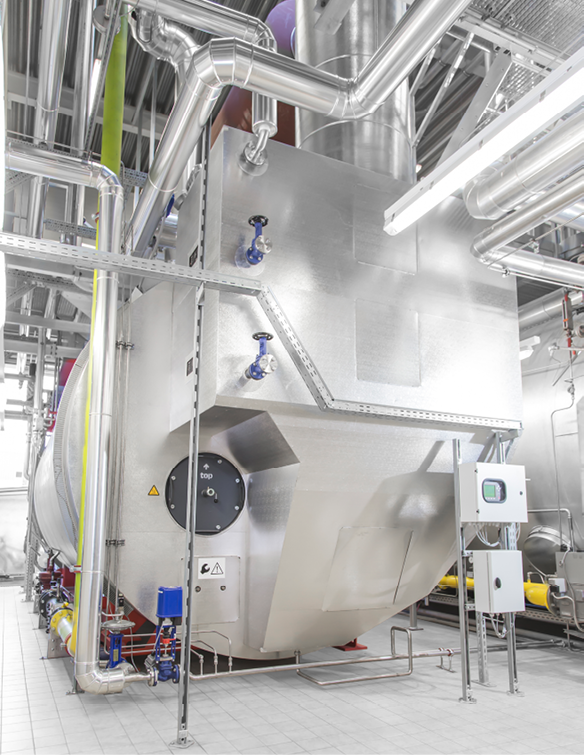
Aislamiento desmontable en las aberturas de inspección (UL-S con economizador integrado)
Válvulas aisladas
Las válvulas se encuentran en muchos puntos de los sistemas de calderas de vapor y son necesarias para el funcionamiento y el mantenimiento. Por motivos de instalación o de coste, o debido a diversos límites de suministro, en los sistemas nuevos se sigue omitiendo con frecuencia el aislamiento de las válvulas o de las bridas adaptadoras. Del mismo modo, también es frecuente encontrar válvulas sin aislar en los sistemas existentes.
Sin embargo, a través de estas zonas sin aislar se pierde una gran cantidad de energía. La siguiente tabla puede utilizarse para calcular la energía que se pierde a través de una válvula sin aislar.
Diámetro nominal del tubo |
DN 50 |
DN 65 |
DN 80 |
DN 100 |
DN 125 |
DN 150 |
DN 200 |
DN 250 |
|
Longitud según EN 558 serie 1 |
[mm] |
230 |
290 |
310 |
350 |
400 |
480 |
600 |
730 |
Pérdida de calor, sin aislamiento |
[W] |
224 |
343 |
419 |
586 |
795 |
1,119 |
1,800 |
2,728 |
Pérdida de calor, aislado |
[W] |
21 |
27 |
29 |
33 |
43 |
58 |
88 |
127 |
Ahorro |
[W] |
202 |
316 |
390 |
553 |
752 |
1,061 |
1,712 |
2,601 |
Pérdida de calor con 8,000 Bh/a |
[kWh/a] |
1,619 |
2,527 |
3,117 |
4,425 |
6,018 |
8,489 |
13,693 |
20,810 |
Ahorro con 4.5ct/kWh |
[€/a] |
73 |
114 |
140 |
199 |
270 |
382 |
616 |
936 |
Pérdidas de calor y costes de operación de válvulas no aisladas (temperatura media 200°C)
Información sobre la mesa:
- Temperatura del medio 200°C
- Cálculo de las pérdidas de calor en las tuberías según VDI 2055 hoja 1
- Conversión de las pérdidas de calor en las tuberías en pérdidas de calor en las válvulas con un factor lineal de 1.6 para las válvulas aisladas y un factor lineal de 2 para las válvulas no aisladas. (Esto da como resultado unas pérdidas de calor mucho más conservadoras para las válvulas no aisladas y un ahorro menor que cuando se utiliza el método de cálculo según VDI 2055 hoja 1).
- Longitud de la válvula según EN 558 serie 1
Con una temperatura media de 200°C y un diámetro nominal de válvula de DN 100, se consigue una reducción de la pérdida de calor de aproximadamente 550 W aislando las válvulas. Con un diámetro nominal de DN 150, la pérdida es de aproximadamente 1,060 W. El coste de €100 – 200 por aislar una válvula se amortiza en un año.
Como todo un sistema de vapor requiere válvulas en muchos puntos, el potencial total basado en el aislamiento de las válvulas del sistema de vapor y condensado es, por término medio, de aproximadamente el 1 – 5% del consumo de combustible.